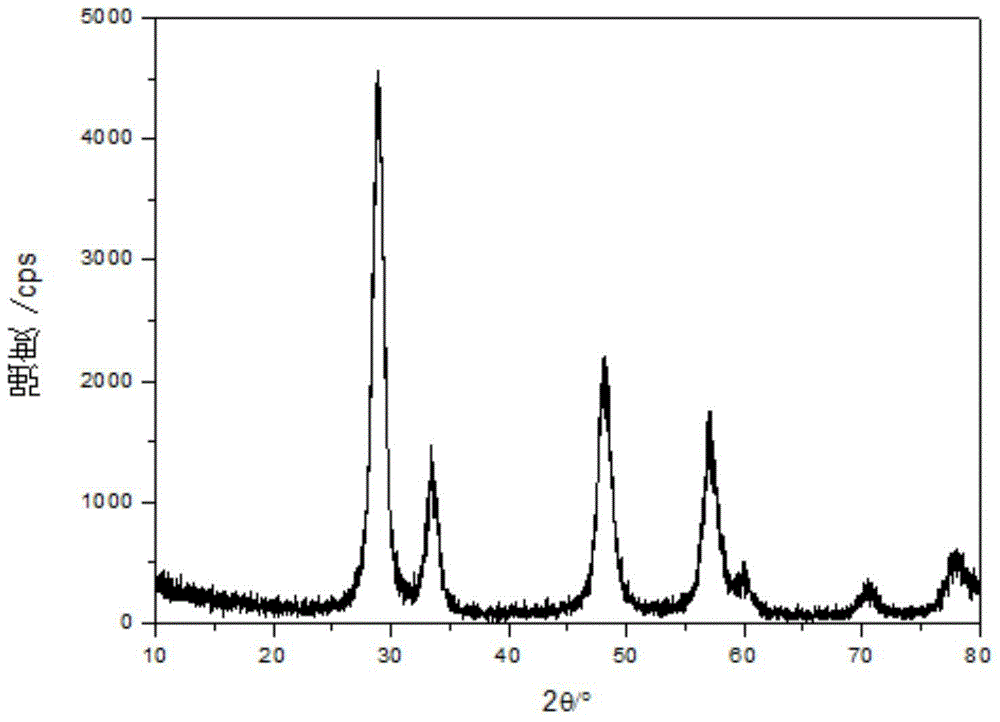
本發(fā)明屬于催化劑領(lǐng)域,涉及一種機(jī)動車尾氣凈化催化材料的制備方法,具體涉及一種鈰鋯基固溶體的制備方法。
背景技術(shù):減少汽車尾氣污染、保護(hù)大氣環(huán)境質(zhì)量,實現(xiàn)生態(tài)環(huán)境和社會的可持續(xù)發(fā)展,是目前及未來相當(dāng)長時間內(nèi)我國環(huán)境保護(hù)的重要課題之一。為了減少污染,必須從提高汽油品質(zhì)、改善發(fā)動機(jī)燃燒狀態(tài)和增加尾氣凈化催化效率三方面進(jìn)行突破。到目前為止,使用汽車尾氣凈化催化劑是最有效途徑就是通過三元催化裝置來降低尾氣中HC、CO和NOx三種有毒氣體的含量,而鈰鋯基固溶體催化材料是三元催化轉(zhuǎn)化裝置中的重要組成部分,它在尾氣凈化過程中起到調(diào)節(jié)氣氛的作用,當(dāng)氣氛處于貧燃狀態(tài)時,鈰鋯基固溶體催化材料將吸收多余的氧氣,當(dāng)氣氛處于富燃狀態(tài)時,鈰鋯基固溶體催化材料放出氧氣,使三種氣體得到有效的轉(zhuǎn)化。因此,鈰鋯基固溶體催化材料的儲氧性能的好壞直接影響尾氣的轉(zhuǎn)化效率。同時鈰鋯基固溶體催化材料可有效穩(wěn)定活性組分的分散,因此具有大的比表面積、較大的孔體積及合適的孔徑分布,并具有良好的抗高溫老化性能、優(yōu)異的低溫催化性能的鈰鋯基儲氧材料成為新三效催化劑的關(guān)鍵材料。由于單純的CeO2在高溫下容易發(fā)生燒結(jié)、顆粒長大,導(dǎo)致比表面積減小,從而降低直至失去儲氧能力。1987年,M.Ozawa等人開始通過添加氧化鋯來改善CeO2的熱穩(wěn)定性。和純的CeO2相比,高性能稀土儲氧材料制備技術(shù)已成為高性能汽車尾氣凈化催化劑的核心技術(shù)和源頭技術(shù),沒有高性能稀土儲氧材料,要制備出具有市場競爭力的汽車尾氣凈化催化劑是不可能的。將ZrO2添加到CeO2中,可形成CeO2-ZrO2固溶體而改善CeO2的體相特性,利于體相氧原子的遷移和擴(kuò)散,使體相反應(yīng)過程變得活潑,能夠提高CeO2的儲氧能力和高溫穩(wěn)定性。同時,Pr、Nd、Y、Nb、La和Ba等稀土及堿土元素的加入可進(jìn)一步增強鈰鋯基固溶體催化材料的抗高溫老化性,提高其儲氧量。中國專利號為ZL200510115874.2的發(fā)明專利公開了一種高比表面鈰鋯復(fù)合氧化物固溶體組合物及其制備方法,通過添加在沉淀出的懸濁液中添加表面活性劑或胺鹽或無機(jī)銨鹽或乙醇,并高溫晶化,晶化后產(chǎn)品經(jīng)乙醇洗滌,高溫焙燒。但是,上述制備工藝復(fù)雜,同時通過高溫晶化,乙醇洗滌,不利于工業(yè)生產(chǎn),且沉淀時為普通液相沉淀,粒子較大。中國專利公開號為CN101637721B的發(fā)明專利公開了一種多孔釔鈰鋯固溶體及其制備方法,通過加入保護(hù)劑、混合稀土金屬鹽溶液和活性聚苯乙烯微球乳液,常溫沉淀,80-100℃陳化,收集沉淀物、水洗、干燥、焙燒得目標(biāo)產(chǎn)物。但是上述制備方法中,聚苯乙烯微球乳液與金屬鹽溶液無法混合均勻,容易降低產(chǎn)品的均一穩(wěn)定性。中國專利公開號為CN100496745C的發(fā)明專利公開了一種線狀或棒狀多晶Ce0.6Zr0.3Y0.1O2固溶體制備方法,通過加入十六烷基三甲基溴化銨作為表面活性。美國專利號為US5,747,401的發(fā)明專利和美國專利專利號為US5,723,101的發(fā)明專利公開了采用共水熱分解法或共沉淀法得到混合沉淀物,然后用烷氧化合物溶液進(jìn)行洗滌或浸漬,得到固溶體具有高比表面、均勻粒子分布和高儲氧能力。所用鈰溶液為四價(可由電解氧化、硝酸鈰銨或溶解碳酸鹽加雙氧水獲得),Ce+4濃度大于85%,900℃,6小時,比表面積為51.7m2/g。但是,上述制備方法通過水熱處理,需要高壓設(shè)備,不利于產(chǎn)業(yè)化生產(chǎn)。因此,特別需要一種鈰鋯基固溶體及其制備方法,以解決上述現(xiàn)有存在的問題。
技術(shù)實現(xiàn)要素:本發(fā)明要解決的技術(shù)問題,是提供一種鈰鋯基固溶體的制備方法,所制備出的鈰鋯基固溶體具有比表面積大、高溫抗老化能力好、儲放氧能力高等特點。為解決上述技術(shù)問題,本發(fā)明所采取的技術(shù)方案是:一種鈰鋯基固溶體的制備方法,它按照如下步驟順序進(jìn)行:(1)Ce4+的制備:將硝酸鈰溶解與水,加熱至70~80℃,在攪拌條件下,用質(zhì)量濃度為10~15%的氨水沉淀至pH為5~6,加入硝酸鈰質(zhì)量0.6~0.7倍的質(zhì)量濃度30%的雙氧水,然后繼續(xù)用氨水沉淀至pH為8.5~9.0,煮沸保溫1.5~2.0h;板框壓濾后,得到稀土總量為25~30%的氫氧化鈰濕餅;將氫氧化鈰濕餅與純水按照質(zhì)量比1:5的比例打漿,用硝酸調(diào)節(jié)pH為1.5~2.5,靜置3~5h后,真空抽濾,得Ce4+的澄清溶液A;(2)活性組分溶液的配制:在Ce4+的澄清溶液A中,加入除鈰以外的其他稀土氧化物的硝酸鹽、硝酸氧鋯,加入有機(jī)絡(luò)合劑,得活性組分溶液B;(3)沉淀反應(yīng):將活性組分溶液B加熱至70~80℃,在攪拌條件下,緩慢加入質(zhì)量濃度為10~15%的氨水,至沉淀終點pH為8.5~9,保溫2~4h;靜置12h后,抽取上層清液,得固液混合漿液C;(4)表面改性:在固液混合漿液C中加入分子量為4000~7000的聚丙烯酸,攪拌1~2h,得到表面改性的物料D;(5)焙燒:將表面改性的物料D在700~750℃下焙燒4~6h,最終制得鈰鋯基固溶體。作為本發(fā)明的一種限定,所述步驟(1)中硝酸鈰質(zhì)量占硝酸鈰與水總質(zhì)量的25~35%。作為本發(fā)明的另一種限定,所述步驟(2)中,所述的除鈰以外的其他稀土氧化物的硝酸鹽,為氧化鑭、氧化釔、氧化鐠和氧化釹對應(yīng)的硝酸鹽中的兩種或三種。作為上述限定的進(jìn)一步限定,所述除鈰以外的其他稀土氧化物以質(zhì)量計,加入量為硝酸鈰用量的0.3~0.32倍。作為本發(fā)明的第三種限定,所述步驟(2)中,所述的硝酸氧鋯的加入量,以質(zhì)量計,為硝酸鈰用量的1.17~1.53倍。作為本發(fā)明的第四種限定,所述步驟(2)中,所述的有機(jī)絡(luò)合劑為羥基羧酸類化合物。作為上述限定的進(jìn)一步限定,所述的羥基羧酸類化合物為α-羥基異丁酸、乳酸、α-羥基醋酸中的一種或兩種。作為上述限定的更進(jìn)一步限定,所述羥基羧酸類化合物的加入量,以質(zhì)量計,為硝酸鈰用量的10~20%。作為本發(fā)明的第五種限定,所述步驟(4)中,所述的聚丙烯酸,以質(zhì)量計,加入量為硝酸鈰用量的1~2%。本發(fā)明還有一種限定,所制得的鈰鋯基固溶體由氧化鈰、氧化鋯和除鈰鋯以外的其它稀土氧化物組成的復(fù)合氧化物組成,其重量百分比如下:氧化鈰:40~50%,和除鈰鋯以外其它稀土氧化物:12~13%,其余為氧化鋯。由于現(xiàn)有的鈰鋯基固溶體的制備方法有很多種,主要是液相法,包括共沉淀法、溶膠凝膠法、模版法、微乳液法等。而共沉淀法作為常用的制備方法,是將沉淀劑加入到金屬的鹽溶液中,將可溶性的組分轉(zhuǎn)化為難溶性組分,經(jīng)過濾、洗滌、干燥、焙燒等步驟得到目標(biāo)化合物,但是在高溫下焙燒會導(dǎo)致比表面積的下降,另外在沉淀、干燥、焙燒等過程中會涉及到粒子的聚集長大、孔徑孔容的合理選擇等。因此本發(fā)明中所涉及的制備方法中的技術(shù)參數(shù)對于最終制備的產(chǎn)品鈰鋯基固溶體的指標(biāo)具有顯著的影響。另外,在制備過程中料液濃度、化學(xué)反應(yīng)的溫度、沉淀劑的濃度、各種添加劑的篩選與添加量的控制等等均是材料制備的關(guān)鍵因素,這涉及到沉淀物的粒度、均勻性、分散性、沉降性等,也涉及到目標(biāo)產(chǎn)品的聚集性、形貌、固溶性、孔徑孔容等。由于采用了上述的技術(shù)方案,本發(fā)明與現(xiàn)有技術(shù)相比,所取得的技術(shù)進(jìn)步在于:(1)先制備Ce4+,然后與其他稀土離子及+4價的鋯離子混合,得到混合金屬硝酸鹽溶液,本發(fā)明通過混合金屬硝酸鹽溶液含有有機(jī)絡(luò)合劑,通過有機(jī)絡(luò)合劑與稀土及鋯離子的絡(luò)合配位,控制沉淀反應(yīng)過程中的沉淀速度,得到了粒徑均一、穩(wěn)定的前驅(qū)體。(2)選自與稀土離子配位強的羥基羧酸及價態(tài)高的稀土離子及鋯離子,一方面,作為硬酸類的稀土離子,電荷數(shù)越大,靜電引力大,配位能力強,增加了稀土離子與絡(luò)合基的絡(luò)合能力,提高了絡(luò)合物的穩(wěn)定性;另一方面,促進(jìn)了稀土離子與鋯離子的的固溶能力,確保了目標(biāo)產(chǎn)品具有好的固溶相,即使在1000℃的高溫老化下依然沒有分相。(3)通過聚丙烯酸在沉淀物前驅(qū)體進(jìn)行表面處理,一方面,解決了焙燒過程中顆粒的團(tuán)聚問題;另一方面,通過有機(jī)物的焙燒,提高焙燒產(chǎn)物的孔徑、孔容,得到熱穩(wěn)定性良好的鈰鋯基固溶體催化材料。(4)通過混合金屬料液選擇及濃度、沉淀劑的選擇及濃度、添加劑的篩選及添加量的控制,結(jié)合反應(yīng)的條件、焙燒條件等的適宜選擇和控制,得到了具有顆粒小,比表面積大、高溫抗老化能力和活性高等優(yōu)點的鈰鋯基固溶體催化材料。本發(fā)明適用于鈰鋯基固溶體的制備,尤其適用于機(jī)動車尾氣凈化催化劑、有機(jī)廢氣消除和天然氣催化燃燒等廢氣凈化或催化燃燒的催化劑用載體和助劑。本發(fā)明下面將結(jié)合說明書附圖與具體實施例作進(jìn)一步詳細(xì)說明。附圖說明圖1為本發(fā)明的實施例1制備鈰鋯基固溶體的XRD示意圖。圖2為本發(fā)明的實施例1制備鈰鋯基固溶體1000℃焙燒4h的XRD示意圖。圖3為本發(fā)明的對比例1制備鈰鋯基固溶體1000℃焙燒4h的XRD示意圖。具體實施方式實施例1一種鈰鋯基固溶體的制備方法一種鈰鋯基固溶體的制備方法,它按照如下步驟順序進(jìn)行:(1)Ce4+的制備:將105kg硝酸鈰溶解與315kg水混合,加熱至70℃,在攪拌條件下,用質(zhì)量濃度為10%的氨水沉淀至pH為5,加入63kg質(zhì)量濃度30%的雙氧水,然后繼續(xù)用氨水沉淀至pH為9.0,煮沸保溫2.0h;板框壓濾后,得到氫氧化鈰濕餅160kg(稀土總量為25%);將160kg氫氧化鈰濕餅與800kg純水打漿,用硝酸調(diào)節(jié)pH為1.5,靜置3h后,真空抽濾,得Ce+4的澄清溶液A;(2)活性組分溶液的配制:在Ce4+的澄清溶液A中加入15.7kg硝酸鑭、15.7kg硝酸釔、240kg硝酸氧鋯,10.5kgα-羥基異丁酸,得活性組分溶液B;(3)沉淀反應(yīng):將活性組分溶液B加熱至70℃,在攪拌條件下,緩慢加入質(zhì)量濃度為10%的氨水,至沉淀終點為8.5,保溫2h;靜置12h后,抽取上層清液,得固液混合漿液C;(4)表面改性:在固液混合漿液C中加入1.05kg分子量為4000的聚丙烯酸,攪拌1h,得到表面改性的物料D;(5)焙燒:將表面改性的物料D在700下焙燒6h,得所述的稀鈰鋯基固溶體。鈰鋯基固溶體的組成為氧化鈰40%,氧化鋯48%,6%氧化鑭,6%氧化釔。得到的鈰鋯基固溶體的比表面積為92.5m2/g,經(jīng)XRD分析,見圖1;該催化材料在1000℃焙燒4h后的比表面積為56.2m2/g,經(jīng)XRD分析,見圖2;1050℃焙燒12h后的比表面積為34.5m2/g。實施例2-6鈰鋯基固溶體的制備方法實施例2-6分別為一種鈰鋯基固溶體的制備方法,其方法與實施例1類似,不同之處僅在于其中所涉及的技術(shù)參數(shù)不同,具體如下表所示:對比例1將105kg硝酸鈰、15.7kg硝酸鑭、15.7kg硝酸釔、240kg硝酸氧鋯,加入到1831kg的純水中,溶解澄清,得澄清透明的溶液后,加熱至70℃得澄清透明的溶液A;在攪拌條件下,往溶液A中緩慢加入10%的氨水,至pH為9.0。然后在攪拌條件下,保溫2h后,靜置12h后,抽取上層清液,得固液混合漿液,然后轉(zhuǎn)入匣缽中,在700下焙燒6h,得所述的鈰鋯基固溶體。鈰鋯基固溶體的組成為氧化鈰40%,氧化鋯48%,6%氧化鑭,6%氧化釔。得到的鈰鋯基固溶體的比表面積為80.5m2/g,該催化材料在1000℃焙燒4h后的比表面積為21.2m2/g,1050℃焙燒12h后的比表面積為8.5m2/g。經(jīng)XRD分析,見圖3,1000℃焙燒4h后產(chǎn)品與實施例1(圖2)相比,出現(xiàn)了明顯的分相,并且比表面積較實施例1-6均有明顯下降。對比例2將105kg硝酸鈰、15.7kg硝酸鑭、15.7kg硝酸釔、240kg硝酸氧鋯,加入到1831kg的純水中,溶解澄清,得澄清透明的溶液后,加熱至70℃得澄清透明的溶液A;在攪拌條件下,往溶液A中緩慢加入10%的氨水,至pH為9.0。然后在攪拌條件下,保溫2h后,靜置12h后,抽取上層清液,得固液混合漿液。在固液混合漿液加入1.05kg分子量為4000的聚丙烯酸,攪拌1h,轉(zhuǎn)入匣缽中,在700下焙燒6h,得所述的鈰鋯基固溶體。鈰鋯基固溶體的組成為氧化鈰40%,氧化鋯48%,6%氧化鑭,6%氧化釔。得到的鈰鋯基固溶體的比表面積為80.5m2/g,該催化材料在1000℃焙燒4h后的比表面積為28.2m2/g,1050℃焙燒12h后的比表面積為13.5m2/g。較實施例1-6所值得的鈰鋯基固溶體的在1000℃及1050℃的比表面積均有所下降。對比例3將105kg硝酸鈰溶解與315kg水混合,加熱至70℃,在攪拌條件下,用質(zhì)量濃度為10%的氨水沉淀至pH為5,加入63kg質(zhì)量濃度30%的雙氧水,然后繼續(xù)用氨水沉淀至pH為9,煮沸保溫2h;板框壓濾后,得到氫氧化鈰濕餅160kg(稀土總量為25%);將160kg氫氧化鈰濕餅與800kg純水打漿,用硝酸調(diào)節(jié)pH為1.5,靜置3h后,真空抽濾,得澄清溶液A;在澄清溶液A中,加入15.7kg硝酸鑭、15.7kg硝酸釔、240kg硝酸氧鋯,得活性組分溶液B;將活性組分溶液B加熱至70℃,在攪拌條件下,緩慢加入質(zhì)量濃度為10%的氨水,至沉淀終點為8.5,保溫2h;靜置12h后,抽取上層清液,得固液混合漿液C。在固液混合漿液C中加入1.05kg分子量為4000的聚丙烯酸,攪拌1h,轉(zhuǎn)入匣缽中,在700下焙燒6h,得所述的鈰鋯基固溶體。鈰鋯基固溶體的組成為氧化鈰40%,氧化鋯48%,6%氧化鑭,6%氧化釔。得到的鈰鋯基固溶體的比表面積為92.5m2/g,該催化材料在1000℃焙燒4h后的比表面積為26.2m2/g,1050℃焙燒12h后的比表面積為14.5m2/g,較實施例1-6所值得的鈰鋯基固溶體的在1000℃及1050℃的比表面積均有所下降。以上所述,僅是本發(fā)明的較佳實施例而已,并非是對本發(fā)明作其它形式的限制,任何熟悉本專業(yè)的技術(shù)人員可能利用上述技術(shù)內(nèi)容作為啟示加以變更或改型為等同變化的等效實施例。但是凡是未脫離本發(fā)明技術(shù)方案內(nèi)容,依據(jù)本發(fā)明的技術(shù)實質(zhì)對以上實施例所作出的簡單修改,等同變化與改型,仍屬于本發(fā)明權(quán)利要求的保護(hù)范圍。