專利名稱:一種將電解鋁高溫煙氣中的二氧化碳轉化為甲醇的裝置的制造方法
【專利摘要】本實用新型涉及一種將電解鋁高溫煙氣中的二氧化碳轉化為甲醇的裝置,屬于電解鋁煙氣治理和二氧化碳資源化利用技術領域。該裝置包括氣體轉化爐、脫氟除塵裝置、儲氣罐、合成氣凈化裝置、氣體壓縮機、甲醇合成塔和甲醇分離器,氣體轉化爐的煙氣出口連接脫氟除塵裝置,脫氟除塵裝置的脫氟煙氣出口連接儲氣罐,儲氣罐的氣體出口連接合成氣凈化裝置,合成氣凈化裝置的氣體出口連接氣體壓縮機,氣體壓縮機的氣體出口連接甲醇合成塔,甲醇合成塔的氣體出口連接甲醇分離器,甲醇分離器的氣體出口連接氣體壓縮機的氣體入口。利用本實用新型,可以將電解鋁煙氣中的二氧化碳轉化為甲醇,同時減少污染物排放,實現(xiàn)煙氣余熱利用。
【專利說明】
一種將電解鋁高溫煙氣中的二氧化碳轉化為甲醇的裝置
技術領域
[0001]本實用新型涉及一種將電解鋁高溫煙氣中的二氧化碳轉化為甲醇的裝置,屬于電解鋁煙氣治理和二氧化碳資源化利用技術領域。【背景技術】
[0002]電解鋁生產過程中,伴隨著電化學反應的進行,電解槽中排放出大量的高溫煙氣, 其主要成份為C02,同時含有冊、0?4、31?4、30;^0和粉塵等有害物質。隨著電解鋁行業(yè)節(jié)能減排和環(huán)保要求的日益提高,實現(xiàn)C02資源化利用、減少污染物排放和充分利用煙氣中的余熱,成為電解鋁行業(yè)迫切需要解決的現(xiàn)實問題。本實用新型提出了一種將電解鋁煙氣中的 C02轉化為甲醇的方法,可以同時解決C02資源化利用、污染物治理和煙氣余熱利用問題。
【發(fā)明內容】
[0003]針對上述現(xiàn)有技術存在的問題及不足,本實用新型提供一種將電解鋁高溫煙氣中的二氧化碳轉化為甲醇的裝置。本項實用新型的工藝路線為:將鋁電解槽中排放出的高溫煙氣直接通入氣體轉化爐中,與焦炭發(fā)生反應,使煙氣中的C02轉化為C0,由于該反應是吸熱反應,煙氣中的余熱得到有效利用。從氣體轉化爐中排出的煙氣,經脫氟除塵處理后,與氯堿工藝副產的氫氣混合,得到合成氣,深度脫除合成氣中的硫、氯、氟,然后用壓縮機將合成氣壓縮至8?15MPa,在合成塔中將C0氫化還原為甲醇,然后在甲醇分離器中將甲醇分離出來,未反應氣體經循環(huán)壓縮機返回甲醇合成塔。
[0004]—種將電解鋁高溫煙氣中的二氧化碳轉化為甲醇的裝置,包括氣體轉化爐1、脫氟除塵裝置2、儲氣罐3、合成氣凈化裝置4、氣體壓縮機5、甲醇合成塔6和甲醇分離器7,氣體轉化爐1的煙氣出口連接脫氟除塵裝置2,脫氟除塵裝置2的脫氟煙氣出口連接儲氣罐3,儲氣罐3的氣體出口連接合成氣凈化裝置4,合成氣凈化裝置4的氣體出口連接氣體壓縮機5,氣體壓縮機5的氣體出口連接甲醇合成塔6,甲醇合成塔6的氣體出口連接甲醇分離器7,甲醇分離器7的氣體出口連接氣體壓縮機5的氣體入口。
[0005]所述氣體轉化爐1頂部設有從上至下的焦炭加料斗和焦炭封閉倉,焦炭加料斗和焦炭封閉倉底部均設有煤鎖,氣體轉化爐1底部設有灰渣封閉倉,灰渣封閉倉的上部和下部分別設有灰渣鎖。電解鋁高溫煙氣從氣體轉化爐下部底吹進入,煙氣中的C02遇焦炭后發(fā)生化學反應,生成C0,由于該反應是吸熱反應,使得上升煙氣的溫度逐漸降低,出爐煙氣的溫度降低至300?350°C。在氣體轉化爐中,焦炭與C02發(fā)生反應,生成的灰渣落在氣體轉化爐底部。氣體轉化爐底部設有灰渣鎖,當灰渣達到一定數(shù)量時,打開此灰渣鎖,使灰渣落入灰渣封閉倉中,隨后立即關閉這個灰渣鎖。當灰渣封閉倉中灰渣量達到一定數(shù)量時,打開灰渣封閉倉下部的灰渣鎖,灰渣在重力的作用下從灰渣封閉倉中排出,灰渣封閉倉下部的灰渣鎖隨即關閉。通過這種方法,可以減少有害物質從氣體轉化爐下部外逸,造成廠房工作面環(huán)境污染。氣體轉化爐頂部設有焦炭加料斗和焦炭封閉倉,焦炭加料斗底部設有煤鎖,當焦炭加料斗中加料量達到所需量時,將焦炭加料斗底部的煤鎖打開,焦炭在重力作用下落入焦炭封閉倉中,焦炭加料斗底部的煤鎖隨即關閉。當焦炭封閉倉中的焦炭量達到所需量,且焦炭加料斗底部的煤鎖關閉時,打開焦炭封閉倉底部的煤鎖,焦炭在重力作用下落入氣體轉化爐中,焦炭封閉倉底部的煤鎖隨即關閉。通過這種方法,可以減少有害物質從氣體轉化爐上部加料口外逸,造成廠房工作面環(huán)境污染。氣體轉化爐底部的焦炭優(yōu)先與高溫煙氣發(fā)生反應,中上部的焦炭在重力作用下持續(xù)下行,新焦炭從氣體轉化爐上部加入,生成的灰渣從氣體轉化爐底部排出。
[0006]所述氣體轉化爐1高度為1.8?2米,直徑為0.3?0.35米,氣體轉化爐1內壁襯有耐火材料。
[0007]一種將電解鋁高溫煙氣中的二氧化碳轉化為甲醇的方法:將電解鋁高溫煙氣通入裝有焦炭的氣體轉化爐中,使煙氣中的二氧化碳轉化為一氧化碳,然后將氣體轉化爐中排出的煙氣進行脫氟除塵處理,再與氯堿工藝副產的氫氣混合,得到合成氣,將合成氣通入氣體凈化裝置中,深度脫除其中的硫、氯、氟,然后將合成氣壓縮至8?15MPa,在甲醇合成塔中制備甲醇。
[0008]其步驟如下:
[0009]步驟一、在電解鋁生產過程中,將電解槽排放出的高溫煙氣直接通入氣體轉化爐1 中,使煙氣中的C02與焦炭發(fā)生反應,生成C0;
[0010]步驟二、將經步驟一得到的含⑶的煙氣通入脫氟除塵裝置2中,進行脫氟除塵處理;
[0011]步驟三、將經步驟二得到的含有C0的煙氣通入儲氣罐3中,與氯堿工藝副產的氫氣混合,得到合成氣;
[0012]步驟四、將步驟三得到的合成氣通入合成氣凈化裝置4中,得到深度脫除硫、氯、氟的合成氣;
[0013]步驟五、將步驟四得到的深度脫除硫、氯、氟的合成氣用氣體壓縮機5壓縮至為8? 15MPa,然后送入甲醇合成塔6中制甲醇;
[0014]步驟六、將步驟五得到的甲醇送入到甲醇分離器7中,冷凝分離出甲醇,未反應氣體經氣體壓縮機5重新返回到甲醇合成塔6中。
[0015]所述步驟二的脫氟除塵處理方法為:將步驟一得到的含有C0的煙氣,在排煙管內與氧化鋁粉末充分接觸,得到載氟氧化鋁和煙氣,再經布袋收塵,得到脫氟煙氣。
[0016]所述步驟二的脫氟除塵處理方法為:將步驟一得到的含有C0的煙氣從氣體洗滌塔底部通入,用濃度為5wt%的Na2C〇3水溶液噴淋洗滌,得到脫氟煙氣。[0〇17]在煙氣洗滌塔中,用5wt%的Na2C037K溶液溶解吸收煙氣中的HF、S02和C02,涉及的主要反應有:
[0018]Na2C〇3+2HF=2NaF+C〇2+H20
[0019]Na2C〇3+S〇2=Na2S〇3+C〇2
[0020]Na2C〇3+C〇2+H20=2 NaHCOs
[0021]煙氣中的顆粒物質隨洗滌過程除去。[〇〇22]洗滌液經多次反復使用,當其中的氟化鈉濃度累積到20?30g/L時,將洗滌液進行過濾,然后在濾液中加入鋁酸鈉溶液,由于煙氣中的HF、S02、C02氣體被Na2C03水溶液溶解吸收,濾液呈中性或弱酸性,向濾液加入鋁酸鈉,鋁酸鈉轉化成為氫氧化鋁,氫氧化鋁與氟化鈉反應,生成三氟化鋁,三氟化鋁與氟化鈉反應,生成冰晶石,所得冰晶石返回鋁電解槽循環(huán)使用。涉及的主要反應如下:
[0023]Al(0H)3+3NaF=AlF3+3Na0H
[0024]AlF3+3NaF=Na3AlF6[〇〇25](1)硫的脫除方法[〇〇26] 在脫硫器中,用氧化鋅脫除合成氣中的硫化物和硫醇,操作溫度為200?350°C。 [〇〇27](2)氯、氟的脫除方法[〇〇28]在脫氯氟反應器中,采用主要成分為Zn0/Al203/Ca0的脫氯氟劑脫除合成氣中的氯化物和氟化物,操作溫度為200?350 °C。
[0029]根據實際氣體成分及含量,可將脫硫劑和脫氯氟劑置于同一反應器中,連續(xù)脫除硫、氯、氟,操作溫度為200?350°C。
[0030]在甲醇合成塔6中,控制反應溫度為230?290°C,采用工業(yè)制甲醇的銅基催化劑, 將一氧化碳催化氫化為甲醇。[0031 ]與現(xiàn)有技術相比,本實用新型具有以下優(yōu)勢:
[0032](1)現(xiàn)有電解鋁生產工藝,電解槽中排放出的高溫煙氣,其主要成份為⑶2,同時含有冊、0?4、31?4、302、0)和粉塵等有害物質,因此,電解鋁行業(yè)普遍存在二氧化碳排放量大、 污染物治理難度高、余熱損失嚴重等問題。利用本實用新型提出的方法,可以將電解鋁煙氣中的二氧化碳轉化為甲醇,同時減少污染物排放,實現(xiàn)煙氣余熱利用。[〇〇33](2)現(xiàn)有氯堿生產工藝,陰極反應生成大量氫氣,由于氫氣具有易燃易爆、難儲難運的特點,因此,氯堿行業(yè)有40%的氫氣因無法有效利用而被排空。利用本項專利提出的方法,可以將電解鋁煙氣中的二氧化碳轉化為一氧化碳,然后用氯堿工藝副產的氫氣將一氧化碳氫化還原為甲醇,通過這種方法,可以達到產業(yè)優(yōu)化組合的效果。[〇〇34](3)現(xiàn)有甲醇生產工藝,采用的主要含碳原料為煤和天然氣,所生成的甲醇其碳源全部來自于化石燃料;利用本項專利提出的方法,采用電解鋁煙氣中的二氧化碳和煤為原料生產甲醇,所生成的甲醇其碳源一半來自于二氧化碳,一半來自于化石燃料,前者屬于碳資源循環(huán)利用,通過碳資源循環(huán)利用,可以減少化石燃料使用量,籍此可以減少二氧化碳排放?!靖綀D說明】
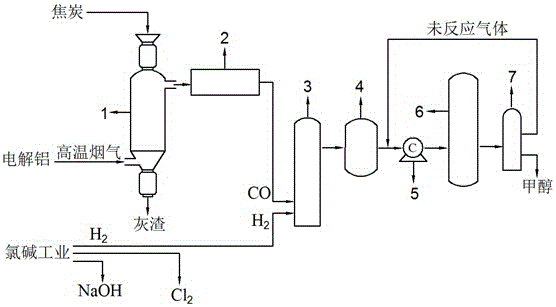
[0〇35]圖1是本實用新型裝置不意圖。
[0036]圖中:1-氣體轉化爐,2-脫氟除塵裝置,3-儲氣罐,4-合成氣凈化裝置,5-氣體壓縮機,6-甲醇合成塔,7-甲醇分離器?!揪唧w實施方式】
[0037]下面結合附圖和【具體實施方式】,對本實用新型作進一步說明。
[0038]實施例1
[0039]如圖1所示,將電解鋁高溫煙氣中的二氧化碳轉化為甲醇的裝置,包括氣體轉化爐 1、脫氟除塵裝置2、儲氣罐3、合成氣凈化裝置4、氣體壓縮機5、甲醇合成塔6和甲醇分離器7, 氣體轉化爐1的煙氣出口連接脫氟除塵裝置2,脫氟除塵裝置2的氣體出口連接儲氣罐3,儲氣罐3的氣體出口連接合成氣凈化裝置4,合成氣凈化裝置4的氣體出口連接氣體壓縮機5, 氣體壓縮機5的氣體出口連接甲醇合成塔6,甲醇合成塔6的氣體出口連接甲醇分離器7,甲醇分離器7的氣體出口連接氣體壓縮機5的氣體入口。
[0040]其中氣體轉化爐1頂部設有從上至下的焦炭加料斗和焦炭封閉倉,焦炭加料斗和焦炭封閉倉底部均設有煤鎖,氣體轉化爐1底部設有灰渣封閉倉,灰渣封閉倉的上部和下部分別設有灰渣鎖;氣體轉化爐1高度為1.8米,直徑為0.3米,氣體轉化爐1內壁襯有耐火材料。
[0041]將電解鋁高溫煙氣中的二氧化碳轉化為甲醇的方法,其步驟如下:
[0042]步驟一、在電解鋁生產過程中,將電解槽中排放出的高溫煙氣直接通入氣體轉化爐1中,使煙氣中的C02與焦炭發(fā)生反應,生成C0,每次向氣體轉化爐加入焦炭的量為12千克,高溫煙氣的通入量為〇.45立方米/分鐘;
[0043]步驟二、將經步驟一得到的含有C0的煙氣通入脫氟除塵裝置2中,煙氣在排煙管內與氧化鋁粉末充分接觸,使煙氣中的氟化物吸附在氧化鋁表面,形成載氟氧化鋁,排煙管前段上部設有高位倉,高位倉中裝有氧化鋁粉末,氧化鋁粉末從高位倉底部出口流出,落入排煙管內,被煙氣吹拂至呈懸浮態(tài),排煙管末端設有布袋收塵裝置,在布袋收塵裝置中,載氟氧化鋁在重力作用下落入載氟氧化鋁收集倉,煙氣經布袋收塵后,脫除其中的煙塵,得到主要成分為C0的氣體。
[0044]步驟三、將經步驟二得到的氣體通入到儲氣罐3中,與氯堿工藝副產的氫氣混合, 得到體積比CO: H2=l: 2.2的合成氣;
[0045]步驟四、將經步驟三得到的合成氣通入合成氣凈化裝置4中,先在脫硫反應器中用氧化鋅脫除硫化物和硫醇,操作溫度為200?350°C,再在脫氯氟反應器中,采用主要成分為 ZnO/Al2〇3/CaO的脫氯氟劑,脫除合成氣中的氯化物和氟化物,操作溫度為200?350°C ;
[0046]步驟五、將步驟四得到的深度脫除硫、氯、氟的合成氣通過氣體壓縮機5,將氣體壓縮至8MPa,然后送入甲醇合成塔6中,在250°C的溫度下,采用工業(yè)制甲醇的銅基催化劑,將 C0氫化還原為甲醇;
[0047]步驟六、將步驟五得到的甲醇送入到甲醇分離器7中,冷凝分離出甲醇,未反應氣體經氣體壓縮機5重新返回到甲醇合成塔6中。
[0048]實施例2
[0049]如圖1所示,該將電解鋁高溫煙氣中的二氧化碳轉化為甲醇的裝置,包括氣體轉化爐1、脫氟除塵裝置2、儲氣罐3、合成氣凈化裝置4、氣體壓縮機5、甲醇合成塔6和甲醇分離器 7,氣體轉化爐1的煙氣出口連接脫氟除塵裝置2,脫氟除塵裝置2的氣體出口連接儲氣罐3, 儲氣罐3的氣體出口連接合成氣凈化裝置4,合成氣凈化裝置4的氣體出口連接氣體壓縮機 5,氣體壓縮機5的氣體出口連接甲醇合成塔6,甲醇合成塔6的氣體出口連接甲醇分離器7, 甲醇分離器7的氣體出口連接氣體壓縮機5的氣體入口。
[0050]其中氣體轉化爐1頂部設有從上至下的焦炭加料斗和焦炭封閉倉,焦炭加料斗和焦炭封閉倉底部均設有煤鎖,氣體轉化爐1底部設有灰渣封閉倉,灰渣封閉倉的上部和下部分別設有灰渣鎖,氣體轉化爐1高度為2米,直徑為0.35米,氣體轉化爐1內壁襯有耐火材料。
[0051]將電解鋁高溫煙氣中的二氧化碳轉化為甲醇的方法,其步驟如下:[〇〇52]步驟一、在電解鋁生產過程中,將電解槽中排放出的高溫煙氣直接通入氣體轉化爐1中,使煙氣中的C〇2與焦炭發(fā)生反應,生成CO,每次向氣體轉化爐中加入焦炭的量為14千克,高溫煙氣的通入量為〇.42立方米/分鐘;[〇〇53]步驟二、將經步驟一得到的含有⑶的煙氣,通入脫氟除塵裝置2中,用濃度為5wt% 的Na2C03水溶液進行洗滌,煙氣從洗滌塔底部通入,通入量為0.8立方米/分鐘,洗滌液從洗滌塔上部噴淋,流量為0.12立方米/分鐘,經脫氟除塵后的煙氣,從洗滌塔頂部排出,洗滌液反復多次使用,至洗滌液中氟化鈉濃度達到20?30g/L,將洗滌液進行過濾,然后在濾液中加入鋁酸鈉溶液,由于濾液呈中性或弱酸性,鋁酸鈉轉化成為氫氧化鋁,氫氧化鋁與氟化鈉反應,生成三氟化鋁,三氟化鋁與氟化鈉反應,生成冰晶石,所得冰晶石返回鋁電解槽循環(huán)使用;[〇〇54]步驟三、將經步驟二得到的氣體通入到儲氣罐3,與氯堿工藝副產的氫氣混合,得到體積比CO: H2=1:2.3的合成氣;
[0055]步驟四、將步驟三得到的合成氣通入到合成氣凈化裝置4中,用氧化鋅脫除其中的硫化物和硫醇,控制操作溫度為200?350°C,然后在脫氯氟反應器中,用主要成分為ZnO/ Al2〇3/CaO的脫氯氟劑脫除合成氣中的氯化物和氟化物,控制操作溫度為200?350°C ;
[0056]步驟五、將步驟四得到的深度脫除硫、氯、氟的合成氣通人氣體壓縮機5,將合成氣壓縮至15MPa,然后通入甲醇合成塔6中,在260°C的溫度下,采用工業(yè)制甲醇的銅基催化劑, 將C0氫化還原為甲醇;[〇〇57] 步驟六、將步驟五得到的氣體送入到甲醇分離器7中,冷凝分離出甲醇,未反應氣體經氣體壓縮機5重新返回到甲醇合成塔6。
[0058]實施例3
[0059]如圖1所示,將電解鋁高溫煙氣中的二氧化碳轉化為甲醇的裝置,包括氣體轉化爐 1、脫氟除塵裝置2、儲氣罐3、合成氣凈化裝置4、氣體壓縮機5、甲醇合成塔6和甲醇分離器7, 氣體轉化爐1的煙氣出口連接脫氟除塵裝置2,脫氟除塵裝置2的氣體出口連接儲氣罐3,儲氣罐3的氣體出口連接合成氣凈化裝置4,合成氣凈化裝置4的氣體出口連接氣體壓縮機5, 氣體壓縮機5的氣體出口連接甲醇合成塔6,甲醇合成塔6的氣體出口連接甲醇分離器7,甲醇分離器7的氣體出口連接氣體壓縮機5的氣體入口。
[0060]其中氣體轉化爐1頂部設有從上至下的焦炭加料斗和焦炭封閉倉,焦炭加料斗和焦炭封閉倉底部均設有煤鎖,氣體轉化爐1底部設有灰渣封閉倉,灰渣封閉倉的上部和下部分別設有灰渣鎖,氣體轉化爐1高度為1.9米,直徑為0.32米,氣體轉化爐1內壁襯有耐火材料。
[0061]將電解鋁高溫煙氣中的二氧化碳轉化為甲醇的方法,其步驟如下:
[0062]步驟一、在電解鋁生產過程中,將電解槽中排放出的高溫煙氣直接通入氣體轉化爐1中,使煙氣中的C02與焦炭發(fā)生反應,生成C0,每次向氣體轉化爐加入焦炭的量為13千克,高溫煙氣的通入量為〇.43立方米/分鐘;
[0063]步驟二、將步驟一得到的含有⑶的煙氣,通入脫氟除塵裝置2中,用濃度為5wt%的 Na2C03水溶液進行洗滌,煙氣從洗滌塔底部通入,通入量為0.78立方米/分鐘,洗滌液從洗滌塔上部噴淋,流量為0.13立方米/分鐘,經脫氟除塵后的煙氣,從洗滌塔頂部排出,洗滌液反復多次使用,至洗滌液中氟化鈉濃度達到20?30g/L,將洗滌液進行過濾,然后在濾液中加入鋁酸鈉溶液,由于濾液呈中性或弱酸性,鋁酸鈉轉化成為氫氧化鋁,氫氧化鋁與氟化鈉反應,生成三氟化鋁,三氟化鋁與氟化鈉反應,生成冰晶石,所得冰晶石返回鋁電解槽循環(huán)使用;
[0064]步驟三、將經步驟二得到的氣體通入到儲氣罐3,與氯堿工藝副產的氫氣混合,得到體積比CO: H2=l: 2.1的合成氣;
[0065]步驟四、將步驟三得到的合成氣通入到合成氣凈化裝置4中,用氧化鋅脫除其中的硫化物和硫醇,控制操作溫度為200?350°C,然后在脫氯氟反應器中,用主要成分為ZnO/ Al2〇3/CaO的脫氯氟劑脫除合成氣中的氯化物和氟化物,控制操作溫度為200?350°C ;
[0066]步驟五、將步驟四得到的深度脫除硫、氯、氟的合成氣通人氣體壓縮機5,將合成氣壓縮至12MPa,然后通入甲醇合成塔6中,在240°C的溫度下,采用工業(yè)制甲醇的銅基催化劑, 將C0氫化還原為甲醇;
[0067]步驟六、將步驟五得到的氣體送入到甲醇分離器7中,冷凝分離出甲醇,未反應氣體經氣體壓縮機5重新返回到甲醇合成塔6。
[0068]以上結合附圖對本實用新型的【具體實施方式】作了詳細說明,但是本實用新型并不限于上述實施方式,在本領域普通技術人員所具備的知識范圍內,還可以在不脫離本實用新型宗旨的前提下作出各種變化。
【主權項】
1.一種將電解鋁高溫煙氣中的二氧化碳轉化為甲醇的裝置,其特征在于:包括氣體轉 化爐(1)、脫氟除塵裝置(2)、儲氣罐(3)、合成氣凈化裝置(4)、氣體壓縮機(5)、甲醇合成塔 (6)和甲醇分離器(7);氣體轉化爐(1)的煙氣出口連接脫氟除塵裝置(2),脫氟除塵裝置(2) 的氣體出口連接儲氣罐(3),儲氣罐(3)的氣體出口連接合成氣凈化裝置(4),合成氣凈化裝 置(4)的氣體出口連接氣體壓縮機(5),氣體壓縮機的氣體出口連接甲醇合成塔(6 ),甲醇合 成塔的氣體出口連接甲醇分離器(7),甲醇分離器(7)的氣體出口連接氣體壓縮機(5)的氣 體入口。2.根據權利要求1所述的將電解鋁高溫煙氣中的二氧化碳轉化為甲醇的裝置,其特征 在于:所述氣體轉化爐(1)頂部設有從上至下的焦炭加料斗和焦炭封閉倉,焦炭加料斗和焦 炭封閉倉底部均設有煤鎖,氣體轉化爐(1)底部設有灰渣封閉倉,灰渣封閉倉的上部和下部 分別設有灰渣鎖。3.根據權利要求1所述的將電解鋁高溫煙氣中的二氧化碳轉化為甲醇的裝置,其特征 在于:所述氣體轉化爐(1)高度為1.8?2米,直徑為0.3?0.35米,氣體轉化爐(1)內壁襯有 耐火材料。
【文檔編號】B01D53/62GK205710511SQ201620377582
【公開日】2016年11月23日
【申請日】2016年4月29日
【發(fā)明人】施錦, 沈風霞, 戴永年, 宋寧, 王宇棟, 賈友見, 胡玉琪, 楊冬偉, 李青遠, 王琴, 李露
【申請人】昆明理工大學