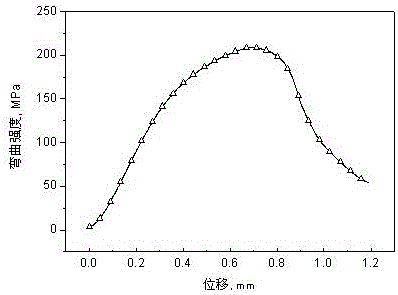
本發(fā)明涉及一種氣氛燒結(jié)多孔結(jié)構(gòu)錳銅高阻尼合金的方法。它是通過以草酸鎳做為鎳元素供體,利用草酸鎳的熱解特性及其分解產(chǎn)物改善燒結(jié)工藝過程,實現(xiàn)大尺寸規(guī)格材料均勻燒結(jié)目的。技術(shù)背景本發(fā)明屬于粉末冶金領(lǐng)域的阻尼材料。錳銅合金作為孿晶型阻尼材料的代表,已被廣泛使用在生活生產(chǎn)的各個領(lǐng)域。錳銅阻尼合金材料具有γ相組織的錳銅合金的反鐵磁轉(zhuǎn)變,形成點陣畸變,觸發(fā)微孿晶,若點陣畸變誘發(fā)了馬氏體相變,則將形成馬氏體孿晶,母相與熱彈性馬氏體相界面的移動和熱彈性馬氏體孿晶亞結(jié)構(gòu)的移動消耗能量,產(chǎn)生高阻尼現(xiàn)象。錳銅阻尼合金材料具有無磁性,低溫阻尼性能很好并且強度和韌性很好的特點。如果成分熱處理得當,其阻尼性能最高可達到橡膠水平。而且錳銅合金材料具有良好的變形能力,可很好的應(yīng)用于阻尼合金支架、阻尼合金墊片、軸承、超傳導(dǎo)線圈、電弓架、阻尼合金薄板等這些零部件上,主要應(yīng)用的錳銅阻尼合金的成分見表1。表1實用化錳銅阻尼合金的成分范圍(質(zhì)量百分比)除了美國的Incramute合金外,其余錳銅合金中都含有元素Ni,其范圍在0.3~5%之間。合金中加入Ni的目的是提高合金的耐蝕性,同時Ni的添加有助于增加Mn-20Cu合金的阻尼性能,但是含量達到5%則無效。錳銅合金時效后的組織產(chǎn)生了微孿晶,微孿晶的出現(xiàn)是在時效過程中由調(diào)幅組織轉(zhuǎn)化而得,合金阻尼性能伴隨著微孿晶密度的增大而提高。Ni含量顯著影響合金fcc-fct轉(zhuǎn)變點Tt,說明Ni能夠抑制高溫γ-Mn相的分解。多孔金屬具有密度低、強度高、吸聲性能高等優(yōu)點逐漸引起人們的注意,金屬材料的多孔化已經(jīng)被證實是提升金屬材料阻尼性能的非常有效途徑之一。MikioFukuhara等人研究了燒結(jié)Mn-(5、10、15、20)Cu合金的阻尼性能,并與鑄造M2052合金進行比較,Mn粉的純度為99%,粒度為16μm,Cu粉的純度為99%,粒度為7μm,混合后在氫氣環(huán)境下30MPa的壓力在950℃溫度下燒結(jié)1h。加熱和冷卻速度分別為0.043和0.028℃/s,熱處理制度為:850℃×1h+450℃×6h。多孔Mn-Cu合金的阻尼性能隨溫度變化(-50~200℃)受的影響比較小,燒結(jié)Mn-Cu合金可以彌補高Mn合金難加工的問題。大同特殊鋼公司申請的Mn系減振合金的制造方法專利(特開2005-68483)(P2005-68483A)是利用Mn粉和Cu-Ni-Fe-Si粉末按照一定的配比混合燒結(jié)得到的MnCu合金的燒結(jié)密度5.9g/cm3,減震系數(shù)可達到0.4。粉末冶金方法制備多孔錳銅合金的基本工藝為采用單質(zhì)或合金化的混合粉末為原料,制成壓坯后在870~950℃在氣氛或真空燒結(jié)、然后800~950℃固溶處理和300~500℃長時間時效處理。單質(zhì)Mn元素與Cu元素擴散形成的一定濃度固溶體在871℃以上溫度會出現(xiàn)瞬態(tài)液相,從而起到液相燒結(jié)的作用,獲得較高強度的合金;但燒結(jié)溫度超過950℃會造成液相過多而不利于燒結(jié)體的形狀穩(wěn)定性。由于氫、氮等氣氛中都富有一定成分的水分壓,會造成錳的表面氧化而阻礙燒結(jié),真空燒結(jié)有利于減輕錳的氧化作用;加壓燒結(jié)或氬等惰性氣體保護燒結(jié)也有類似作用。單質(zhì)錳的導(dǎo)熱系數(shù)只有7.82W/m.℃,純銅為401W/m.℃。由于錳粉的低導(dǎo)熱性,并且其表面或多或少有吸附的氧或水分子,大尺寸壓坯往往表層附近壓制密度高于芯部密度等特點,造成在加熱燒結(jié)過程中坯料中心與表面存在較大的溫差,表面層較早地達到燒結(jié)溫度而致密度提高,芯部達不到燒結(jié)溫度或需要很長的保溫時間,使得大尺寸的錳銅合金燒結(jié)體的組織和性能極不均勻,形成“外熟內(nèi)生”的狀態(tài)。技術(shù)實現(xiàn)要素:本發(fā)明的目的提供一種用草酸鎳改善高錳錳銅阻尼合金燒結(jié)性能的方法。先利用草酸鎳的分解產(chǎn)物做為鎳元素的供體,制備粉末冶金錳銅阻尼合金,鎳含量可以在0.5~5%范圍,再利用草酸鎳熱分解產(chǎn)生的高活性鎳和釋放出來的氣體,促進燒結(jié),并阻止壓坯表面形成致密封閉層,提高燒結(jié)體的均勻性,使得在氫、氬等保護氣氛下燒結(jié)就可以得到大尺寸的錳銅燒結(jié)體。通過后續(xù)熱處理和加工,可獲得低密度、高阻尼錳銅構(gòu)件。具體的制備多孔錳銅高阻尼合金工藝步驟如下:1.粉末準備與混合將電解錳粉(純度:≥99.7%粒度:-100目)、電解銅粉(純度:≥99.7%,粒度:-200目)、水霧化鐵粉(純度:≥98.5%,粒度:~30μm),有時包括霧化鋁粉(純度:≥99.2%,目數(shù):~10μm)、霧化錫粉(純度:≥99.5%,目數(shù):~10μm)、霧化鋅粉(純度:≥99.8%,目數(shù):~10μm)、還原鉬粉(純度:≥99.8%,~1μm)和其他少量單質(zhì)碳、硅、鉻機械破碎粉末,草酸鎳為化學(xué)結(jié)晶晶體粉(純度:≥99%,目數(shù):-80目),按照如下質(zhì)量百分比配料:Mn:45~75Sn:0~1.2Cu:18~46Cr:0~0.6Al:0~5Mo:0~0.9Fe:1~4Zn:0~4Ni*:0.3~5C:0~0.6Si:0~0.8將配好的粉料置于球磨罐中進行干磨,球磨時間為0.5~4h至粉料均勻。由于混合料中有較多量的塑性高的Cu、Sn等,在較大的壓制壓力下會產(chǎn)生塑性變形,從而具有高的壓坯強度,因此一般不需要額外添加成形劑。但當壓坯要求尺寸較大時,可添加一定量的硬脂酸鋅、石蠟微粉等成形劑,可參照一般粉末冶金工藝。2.壓制成型將混好的粉料在100~800MPa的壓力下壓制成所需尺寸的壓坯。壓力范圍根據(jù)坯料的尺寸和粉末混合體的壓制性能,以及孔隙度的要求來選擇,對于大尺寸、孔隙率要求高,取下限;小尺寸、高致密取大壓力。必要時可采取等向壓力的冷等靜壓成形,或者采取松裝燒結(jié)(無壓力)。3.熱解與燒結(jié)過程對于直徑小于等于50mm的小尺寸規(guī)格壓坯,在氫氣、氬氣保護作用下熱解和燒結(jié),具體步驟為200~300℃保溫2~4小時;325~425℃保溫1~4小時;850~950℃保溫時間為1~4小時;升溫速度5~10℃/分鐘。燒結(jié)坯尺寸較小的時候,溫度和保溫時間取下限,升溫速度取上限。草酸鎳添加量大時,熱分解階段保溫時間取上限,升溫速度取下限。對于直徑大于50mm的大尺寸規(guī)格壓坯或大批量生產(chǎn),在熱分解階段采用低壓熱脫脂工藝,即在0.001~0.1KPa的加熱爐進行熱分解;分解過程中通過氫氣,協(xié)助分解殘氣排除。具體步驟為為200~300℃保溫3~6小時;325~425℃保溫3~8小時;升溫速度3~8℃/分鐘。燒結(jié)過程通氫燒結(jié),工藝為870~950℃保溫時間為3~6小時;升溫速度3~8℃/分鐘。4.熱處理工藝燒結(jié)錳銅經(jīng)過固溶和時效處理,獲得高的阻尼性能,具體參照熔鑄、加工和金的工藝參數(shù)。由于采用本發(fā)明制備的錳銅合金為多孔材料,熱處理時加熱時間需要略有延長。草酸鎳在每千克高錳錳銅阻尼合金中的用量為9.3~155克。草酸鎳(NiC2O4·2H2O)常用于制鎳粉和鎳催化劑等,二水草酸鎳在氬氣或真空中的熱分解過程經(jīng)歷了2個階段:①200~300℃時二水草酸鎳失去結(jié)晶水(NiC2O4·2H2O→NiC2O4+2H2O↑);②325~425℃時NiC2O4分解可得到粒度小于1μm的超細鎳粉(NiC2O4→Ni+2CO2↑)。并且在分解溫度范圍內(nèi),由于得到的粉末顆粒很細小而表面能高,鎳粉表面會出現(xiàn)熔融,顆粒之間會出現(xiàn)粘接。在制備含鎳的錳銅合金粉末冶金工藝中,采用草酸鎳代替鎳粉做為鎳元素的供體的主要作用是:①草酸鎳熱分解產(chǎn)生的微細鎳元素具有低的熔點,能夠在較低的溫度將單質(zhì)錳粉熔合,從而減少熱阻界面,提高燒結(jié)坯料的熱導(dǎo)性和溫度均勻性,從而提高錳銅燒結(jié)合金的均勻性;②在草酸鎳分解的溫度范圍,壓坯表面還沒有實現(xiàn)燒結(jié)致密化,因此草酸鎳分解產(chǎn)生的水和二氧化碳氣體不斷排出壓制坯表面,阻止壓坯表面形成致密封閉層,使表面處于多孔狀態(tài),在低溫加熱階段,有利于混合粉的表面吸附水的排出;在高溫燒結(jié)階段,有利于氫氣進入燒結(jié)體,起到還原少量氧化金屬元素的作用;③草酸鎳為細微粉末,不容易發(fā)生塑性粘接,因此利于成分混合均勻;④分解所得的微細高能狀態(tài)鎳粉,容易跟錳、銅、鐵、鋁等元素發(fā)生燒結(jié)擴散,從而促進液相形成和燒結(jié)過程。本發(fā)明燒結(jié)合金直徑達120mm、長度達300mm,密度為5.18~5.75g/cm3,硬度為46~81HRF,彎曲強度為120~215MPa,均勻性好。通過后續(xù)熱處理和加工,可獲得低密度、高阻尼錳銅構(gòu)件。附圖說明圖1為本發(fā)明實施例3的彎曲強度曲線圖;圖2為本發(fā)明實施例6的斷口形貌圖。下面結(jié)合附圖和具體實施方式對本發(fā)明做進一步的詳細說明。實施例1將錳、銅、鐵、鋁、錫、碳、硅等粉末和草酸鎳按照表2實施例1的成分配料。將配好的粉料置于球磨罐中進行干磨,球磨時間約為2h至粉料均勻。表2實施例錳銅阻尼合金的成分范圍(質(zhì)量百分比)合金元素實施例1實施例2實施例3實施例4實施例5實施例6實施例7Mn56.347.165062527473.6Cu364045.925.935.71920Al2.65.02.01.04.0//Fe2.43.21.04.03.021.8Ni*0.53.20.32.22.554.6Sn0.81.2/////Cr////0.6//Mo//0.30.9///Zn//0.54.02.0//C0.60.13//0.08//Si0.80.11//0.12//采用壓制模具將混好的粉料在600MPa的壓力下壓制成壓坯。在氫氣保護作用下熱解和燒結(jié),具體步驟為300℃保溫2小時;425℃保溫1小時;950℃保溫時間為1小時;升溫速度10℃/分鐘。隨爐冷卻,燒結(jié)錳銅經(jīng)過固溶和時效處理獲得產(chǎn)品。所得燒結(jié)坯的性能列于表3。表3實施例錳銅阻尼合金的尺寸與性能燒結(jié)體形狀尺寸,mm密度,g/cm3硬度,HRF彎曲強度,MPa實施例1方形20*20*505.5946120實施例2圓盤Φ80*405.7561140實施例3圓片Φ46*205.2181215實施例4方形60*80*1605.3372200實施例5圓棒Φ120*3005.1850134實施例6圓柱狀Φ36*605.6567164實施例7方形80*100*2005.2055134實施例2將錳、銅、鐵、鋁、錫、碳、硅等粉末和草酸鎳按照表2實施例2的成分配料。將配好的粉料置于球磨罐中進行干磨,球磨時間約為3h至粉料均勻。采用圓形模具將混好的粉料在300MPa的壓力下壓制成壓坯。采用低壓脫脂爐進行熱分解,爐壓為0.001KPa。具體步驟為為260℃保溫4小時;400℃保溫6小時;升溫速度5℃/分鐘。燒結(jié)過程采用通氫爐燒結(jié),工藝為900℃保溫時間為4小時;升溫速度4℃/分鐘。隨爐冷卻,燒結(jié)錳銅經(jīng)過固溶和時效處理獲得產(chǎn)品。所得燒結(jié)坯的性能列于表3中。實施例3將錳、銅、鐵、鋁、鉬、鋅粉末和草酸鎳按照表2實施例3的成分配料。將配好的粉料置于球磨罐中進行干磨,球磨時間約為0.5h至粉料均勻。采用圓形壓制模具將混好的粉料在800MPa的壓力下壓制成壓坯。在氬氣保護作用下熱解和燒結(jié),具體步驟為200℃保溫4小時;325℃保溫4小時;850℃保溫時間為4小時;升溫速度5℃/分鐘。隨爐冷卻,燒結(jié)錳銅經(jīng)過固溶和時效處理獲得產(chǎn)品。彎曲強度曲線如圖1所示。所得燒結(jié)坯的性能列于表3。實施例4將錳、銅、鐵、鋁、鉬、鋅等粉末和草酸鎳按照表2實施例4的成分配料。將配好的粉料置于球磨罐中進行干磨,球磨時間約為2h至粉料均勻。采用長條形模具將混好的粉料在400MPa的壓力下壓制成壓坯。采用低壓脫脂爐進行熱分解,爐壓為0.01KPa。具體步驟為為300℃保溫3小時;425℃保溫8小時;升溫速度8℃/分鐘。燒結(jié)過程采用通氫爐燒結(jié),工藝為950℃保溫時間為3小時;升溫速度8℃/分鐘。隨爐冷卻,燒結(jié)錳銅經(jīng)過固溶和時效處理獲得產(chǎn)品。所得燒結(jié)坯的性能列于表3中。實施例5將錳、銅、鐵、鋁、鉻、鋅、碳、硅等粉末和草酸鎳按照表2實施例5的成分配料,并添加0.8%的硬脂酸鋅。將配好的粉料置于球磨罐中進行干磨,球磨時間約為4h至粉料均勻。將混好的粉料裝入圓形橡皮套中,在100MPa的壓力下冷等靜壓成形。采用低壓熱脫脂工藝,即在0.1KPa的加熱爐進行熱分解,分解過程中通入氫氣,協(xié)助分解殘氣排除。具體步驟為為250℃保溫4小時;380℃保溫4小時;升溫速度3℃/分鐘。燒結(jié)過程通氫燒結(jié),工藝為870℃保溫時間為6小時;升溫速度3℃/分鐘。隨爐冷卻,燒結(jié)錳銅經(jīng)過固溶和時效處理獲得產(chǎn)品。所得燒結(jié)坯的性能列于表3中。實施例6將錳、銅、鐵和草酸鎳按照表2實施例6的成分配料。將配好的粉料置于球磨罐中進行干磨,球磨時間約為2h至粉料均勻。采用圓形壓制模具將混好的粉料在300MPa的壓力下壓制成壓坯。在氬氣保護作用下熱解和燒結(jié),具體步驟為240℃保溫4小時;365℃保溫4小時;880℃保溫時間為2小時;升溫速度6℃/分鐘。隨爐冷卻,燒結(jié)錳銅經(jīng)過固溶和時效處理獲得產(chǎn)品。斷口形貌如圖2所示。所得燒結(jié)坯的性能列于表3實施例7將錳、銅、鐵等粉末和草酸鎳按照表2實施例7的成分配料,并添加0.6%的石蠟微粉。將配好的粉料置于球磨罐中進行干磨,球磨時間約為3h至粉料均勻。將混好的粉料裝入方形橡皮套中,在200MPa的壓力下冷等靜壓成形。采用低壓熱脫脂工藝,即在0.05KPa的加熱爐進行熱分解,分解過程中通入氫氣,協(xié)助分解殘氣排除。具體步驟為為250℃保溫4小時;380℃保溫4小時;升溫速度5℃/分鐘。燒結(jié)過程通氫燒結(jié),工藝為900℃保溫時間為4小時;升溫速度4℃/分鐘。隨爐冷卻,燒結(jié)錳銅經(jīng)過固溶和時效處理獲得產(chǎn)品。所得燒結(jié)坯的性能列于表3中。當前第1頁1 2 3