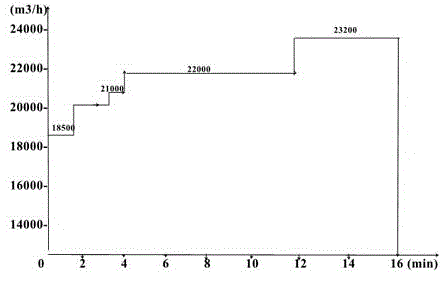
本發(fā)明屬于煉鋼工藝
技術(shù)領(lǐng)域:
,具體公開一種BOF轉(zhuǎn)爐單爐雙鋼冶煉工藝,即單爐次出鋼生產(chǎn)兩種不同鋼種的方法。
背景技術(shù):
:在近代的鋼鐵行業(yè),轉(zhuǎn)爐煉鋼以節(jié)能環(huán)保、優(yōu)質(zhì)低耗、高效穩(wěn)定等諸多優(yōu)勢(shì),越來(lái)越受到現(xiàn)代煉鋼企業(yè)的青睞。面對(duì)復(fù)雜的品種合同,一方面,如何發(fā)揮轉(zhuǎn)爐在優(yōu)鋼向特鋼快速轉(zhuǎn)換的優(yōu)勢(shì)和潛能,打通小批量合同與轉(zhuǎn)爐產(chǎn)能不匹配的生產(chǎn)瓶頸,使得出鋼量為100t的轉(zhuǎn)爐能夠滿足50t合同量的生產(chǎn)需求,這是轉(zhuǎn)爐煉所鋼勢(shì)必面臨的技術(shù)變革;另一方面,要實(shí)現(xiàn)轉(zhuǎn)爐單爐生產(chǎn)兩種不同的鋼種,就必須解決兩次出鋼時(shí)所需面臨的問(wèn)題:⑴爐體傾動(dòng)速度慢,出鋼過(guò)程中帶渣量大,鋼包回磷量高;⑵轉(zhuǎn)爐吹煉工藝不合理,導(dǎo)致終渣回磷率高;⑶出鋼前期擋渣不好,倒?fàn)t時(shí)下渣量增加;⑷擋渣塞命中率低,出鋼后期鋼包下渣量大,回磷量升高;⑸解決兩次出鋼時(shí)載包用的臺(tái)車;⑹轉(zhuǎn)爐出鋼位50t鋼包無(wú)底吹氬氣攪拌設(shè)施,導(dǎo)致出鋼后鋼包底部鋼液凝固。技術(shù)實(shí)現(xiàn)要素:本發(fā)明公開對(duì)一種BOF轉(zhuǎn)爐單爐雙鋼冶煉工藝,通過(guò)解決轉(zhuǎn)爐的設(shè)備及工藝技術(shù)多項(xiàng)創(chuàng)新,最終實(shí)現(xiàn)轉(zhuǎn)爐二次出鋼。本發(fā)明采用如下技術(shù)方案。優(yōu)化爐體傾動(dòng)電機(jī)工藝參數(shù),控制轉(zhuǎn)爐下渣量;優(yōu)化轉(zhuǎn)爐吹煉工藝,改善爐渣成分,減少回磷率;自行設(shè)計(jì)擋渣帽,加強(qiáng)前期擋渣,減少鋼包下渣量;對(duì)擋渣塞材質(zhì)及形狀進(jìn)行調(diào)整,解決命中率不高的問(wèn)題;設(shè)計(jì)雙包位的載包臺(tái)車,解決100t鋼水分別出鋼到雙包(兩個(gè)50t小鋼包)載包臺(tái)車的難題;完善雙包位載包臺(tái)車鋼包吹氬設(shè)施后,使雙包具備吹氬攪拌功能。具體工藝步驟如下:1、調(diào)整爐體傾動(dòng)電機(jī)轉(zhuǎn)速,提高轉(zhuǎn)爐出鋼后回爐速度,減少爐體回傾過(guò)程中的下渣量;2、優(yōu)化轉(zhuǎn)爐氧槍吹煉工藝曲線,減少鋼液過(guò)氧化,合理控制爐渣的成份;3、設(shè)計(jì)耐材質(zhì)擋渣帽,進(jìn)行出鋼前期倒?fàn)t擋渣操作;4、改變擋渣塞密度及擋渣塞外型尺寸,提高擋渣塞命中率;5、改造雙包位出鋼載包臺(tái)車;6、完善雙包為出鋼臺(tái)車吹氬氣設(shè)施,滿足二次出鋼的條件,使雙包位具備吹氬攪拌功能,防止鋼液凝固。本發(fā)明有益效果:1)能夠?qū)嵤┒蔚範(fàn)t出鋼操作,出鋼過(guò)程進(jìn)行兩次擋渣操作;實(shí)現(xiàn)“轉(zhuǎn)爐單爐雙鋼”全新煉鋼工藝路徑,為當(dāng)今世界轉(zhuǎn)爐煉鋼首創(chuàng);2)發(fā)揮轉(zhuǎn)爐在鋼液純凈度方面的優(yōu)勢(shì),優(yōu)化轉(zhuǎn)爐造渣及擋渣工藝,嚴(yán)格控制鋼包平均回磷量為0.0017%,達(dá)到國(guó)內(nèi)同行業(yè)的最好水平;為質(zhì)量提升,開辟新的工藝路徑;3)自2012年起煉鋼廠2#線將原100%由電弧爐生產(chǎn)的合同量的80%~92%,逐步轉(zhuǎn)化為轉(zhuǎn)爐轉(zhuǎn)移鋼水生產(chǎn),滿足客戶對(duì)小批量合同的需求,降低了煉鋼生產(chǎn)成本。附圖說(shuō)明圖1是轉(zhuǎn)爐氧槍吹煉槍位曲線;圖2是轉(zhuǎn)爐氧槍供氧強(qiáng)度曲線;圖3是新設(shè)計(jì)耐材質(zhì)擋渣帽;圖4是改形擋渣塞外形尺寸;圖5是雙包位出鋼載包臺(tái)車及鋼包氬氣底吹裝置。圖標(biāo)說(shuō)明:帽頭1、擋渣帽2、帽尾3、安裝桿4、安裝插孔5、擋渣桿插孔6、擋渣塞7、出鋼導(dǎo)流槽8、50t鋼包9、稱重傳感器10、車輪組11、內(nèi)置氬氣管路12、雙包位臺(tái)車13、減速機(jī)組14。具體實(shí)施方式以下結(jié)合附圖和優(yōu)選實(shí)施例對(duì)本發(fā)明進(jìn)一步說(shuō)明。實(shí)施例11.轉(zhuǎn)爐傾動(dòng)電機(jī)組工藝參數(shù)為電機(jī)額定電流為50HZ,轉(zhuǎn)速589r/min,投產(chǎn)時(shí),電機(jī)執(zhí)行電流為38HZ。轉(zhuǎn)爐第一包出鋼結(jié)束時(shí),因爐內(nèi)仍剩余60t左右的鋼水量,無(wú)法實(shí)施投標(biāo)擋渣操作,經(jīng)測(cè)定在回爐(-92°至-56°)36°區(qū)間內(nèi)的運(yùn)行時(shí)間是6s,由于的現(xiàn)行的電機(jī)運(yùn)行參數(shù)使?fàn)t體傾動(dòng)速度不是特別理想,導(dǎo)致第一包下渣量大,造成鋼包回磷率高,2014年~2015年因轉(zhuǎn)爐一次出鋼下渣量多,導(dǎo)致轉(zhuǎn)移鋼水生產(chǎn)的鋼種大批量成品磷成份不合。為減少出鋼下渣量,合理控制回磷率,提高回爐速度是一項(xiàng)必要措施,將傾動(dòng)電機(jī)輸入電流由原參數(shù)30HZ修改為45HZ,使等距離內(nèi)爐體回傾速度縮短時(shí)間2.55s,現(xiàn)電機(jī)運(yùn)行數(shù)據(jù)見(jiàn)表1;表1調(diào)整傾動(dòng)電機(jī)輸出功率后,出鋼結(jié)束回爐時(shí)間縮短直接減少平均下渣量180kg/爐,轉(zhuǎn)爐終渣渣中五氧化二磷含量為2.4%,減少回磷量為0.003%。2.吹煉工藝優(yōu)化:由于轉(zhuǎn)爐長(zhǎng)期執(zhí)行目前通用的氧槍吹煉工藝暨變槍恒壓吹煉模式,即氧槍開吹及過(guò)程槍位控制在160cm~150cm;氧氣流量恒定控制在23000Nm3/h,使轉(zhuǎn)爐終點(diǎn)碳含量普遍偏低、鋼液過(guò)氧化嚴(yán)重、爐渣中FeT含量較高,使出鋼夾渣或下渣造成鋼包回磷率高,使煉鋼在生產(chǎn)過(guò)程中出現(xiàn)個(gè)別爐號(hào)磷含量超出鋼種規(guī)格范圍。提高終點(diǎn)碳含量、減少鋼液過(guò)氧化問(wèn)題,降低渣中先FeT含量是解決爐渣回磷的關(guān)鍵點(diǎn)。優(yōu)化氧槍吹煉槍位及供氧強(qiáng)度尤為重要,首先是調(diào)整氧槍吹煉槍位,氧槍吹煉槍位曲線見(jiàn)圖1:開吹槍位由原150cm更改為為180cm,后逐步降低150cm;氧槍過(guò)程吹煉槍位控制在150cm~180cm范圍內(nèi),拉碳槍位控制在180cm~140cm,以降低渣中氧化亞鐵含量。另外是氧槍供氧強(qiáng)度見(jiàn)圖2:開吹氧氣流量為18500Nm3/h;1′50″后氧氣流量調(diào)整為20000Nm3/h;3′50″后氧氣流量調(diào)整為21000Nm3/h;4min~12min為吹煉中期階段,氧氣流量控制在22000Nm3/h;吹煉末期拉碳階段氧氣流量由22000Nm3/h調(diào)整到23200Nm3/h。實(shí)現(xiàn)變槍變壓吹煉模式后,轉(zhuǎn)爐中、高碳鋼種的終點(diǎn)控制由工藝改進(jìn)前的平均碳含量0.09%,提高到目前的0.19%~0.26%;同時(shí)低碳鋼種的鋼液過(guò)氧化爐次減少85%;最終減少兩次出鋼過(guò)程中的下渣約120kg/爐。2.1改變?cè)煸贫龋恨D(zhuǎn)爐現(xiàn)行生產(chǎn)過(guò)程要提高爐渣脫磷效果,通常采取的造渣及吹煉工藝手段就是通過(guò)提高爐渣中氧化鐵含量的方法(暨鐵質(zhì)成渣工藝路線),氧化鐵含量控制在18%~22%范圍內(nèi);但高含量氧化鐵的造渣及吹煉制度,也是造成現(xiàn)行轉(zhuǎn)爐高溫出鋼條件下回磷量高達(dá)0.004%左右的主要根源。本發(fā)明通過(guò)采用多元化造渣方式,減少回磷率,渣系優(yōu)化見(jiàn)表2;表2充分發(fā)揮石灰石分解原理:CaCO3=(高溫)CaO+CO2↑,利用吹煉前期180s爐內(nèi)硅、錳元素化學(xué)反應(yīng)快速放熱的條件,當(dāng)溫度達(dá)到1280℃~1400℃,對(duì)加入石灰石實(shí)施前期焙燒以平衡熔池溫度,發(fā)揮轉(zhuǎn)爐終渣氧化鈣效應(yīng),實(shí)施長(zhǎng)效脫磷機(jī)制,弱化爐渣高氧化鐵渣系控制,定量增加石灰石的使用,使轉(zhuǎn)爐爐渣脫磷效果提高。同等鐵水條件下,現(xiàn)造渣制度轉(zhuǎn)爐終點(diǎn)磷含量較原造渣工藝降低0.003%;轉(zhuǎn)爐終渣成份及效果見(jiàn)表3;表3終渣成份CaO,%FeO,%R,堿度終點(diǎn)P,%檢驗(yàn)結(jié)果47.814.63.1降低0.0033.為了保證轉(zhuǎn)移鋼水溫度,滿足低碳鋼種的生產(chǎn)需求,轉(zhuǎn)爐必須高溫、低碳出鋼,造成兩次倒?fàn)t出鋼前期下渣量較大。經(jīng)跟蹤測(cè)量并分別統(tǒng)計(jì)100t鋼包和50t鋼包,在倒?fàn)t時(shí)間一定、下渣量相同的條件下,50t鋼包的回磷率是100t鋼包的2倍。為減少前期倒?fàn)t下渣量,采用新設(shè)計(jì)的擋渣帽(見(jiàn)圖3)進(jìn)行前期擋渣,使下渣量得到有效控制,使用擋渣帽后比未使用擋渣帽的爐次下渣量平均減少230kg/爐。4.轉(zhuǎn)爐在一次倒?fàn)t的出鋼模式中,通常采用擋渣塞擋渣操作方式,鋼包回磷量平均約為0.004%。但對(duì)于兩次倒?fàn)t出鋼模式,由于出鋼時(shí)間延長(zhǎng)、爐渣結(jié)殼現(xiàn)象嚴(yán)重,擋渣塞漂浮直接造成擋渣塞命中率下降(達(dá)到65%),對(duì)擋渣塞材質(zhì)進(jìn)行調(diào)整見(jiàn)表4;表4常規(guī)的擋渣塞與出鋼口磚內(nèi)徑不匹配,倒伏現(xiàn)象嚴(yán)重。改型擋渣塞外形尺寸:高度210mm,錐度為24度;將原豎直式導(dǎo)流槽改為旋轉(zhuǎn)式導(dǎo)流槽;改型后擋渣塞與出鋼口配合緊密,改型的擋渣塞見(jiàn)圖4,投入使用后命中率大幅提高達(dá)到97%,下渣量減少。5.通過(guò)爐下雙包位出鋼臺(tái)車設(shè)備的設(shè)計(jì)和改造(見(jiàn)圖5),滿足二次出鋼條件,實(shí)現(xiàn)了100t轉(zhuǎn)爐一爐鋼水生產(chǎn)兩爐50t異鋼種。6.通過(guò)在轉(zhuǎn)爐出鋼位出鋼臺(tái)車箱體內(nèi)增設(shè)雙包吹氬氣管路(見(jiàn)圖5),實(shí)現(xiàn)了鋼包盛鋼液時(shí)具備吹氬攪拌功能,并調(diào)整氬氣管道壓力為0.7MPa~1.0MPa,解決了鋼包盛鋼過(guò)程中鋼液凝結(jié)問(wèn)題。當(dāng)前第1頁(yè)1 2 3