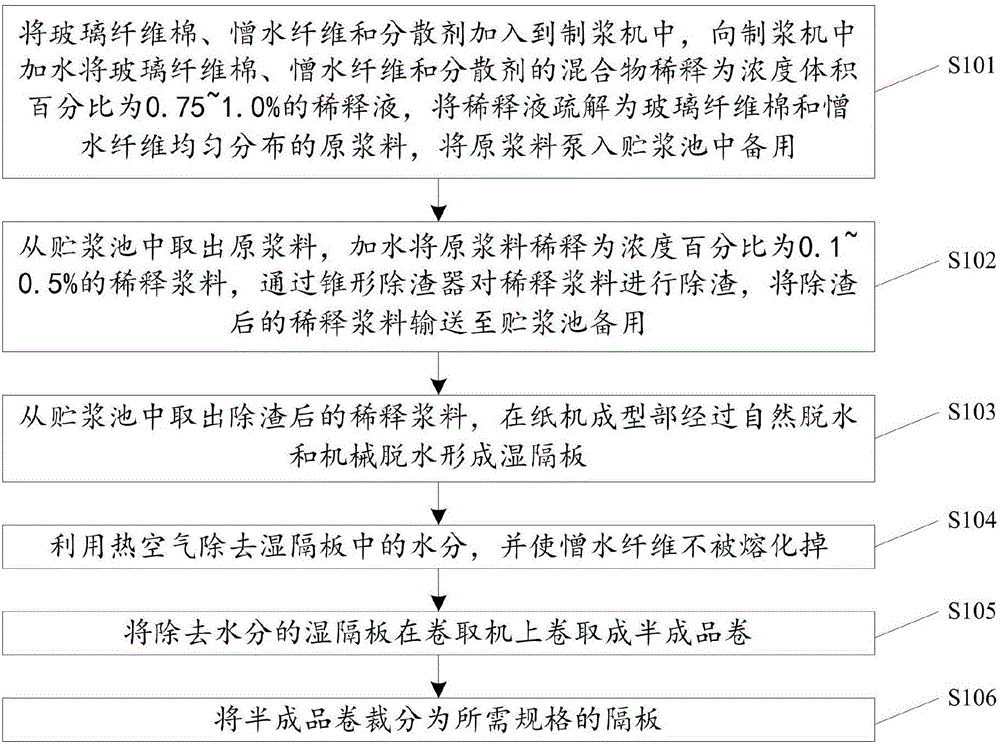
本發(fā)明涉及蓄電池
技術(shù)領(lǐng)域:
,更具體的涉及一種啟停汽車蓄電池隔板及其制備方法。
背景技術(shù):
:啟停汽車隔板是蓄電池的重要組成,不屬于活性物質(zhì),在某些情況下甚至起著決定性的作用,其本身材料為電子絕緣體,而其多孔性使其具有離子導(dǎo)電性。隔板置于電池正負極板之間,既可防止正負極在電解液中發(fā)生短路,貯存電池所需的電解液,同時又能保證電解液在正負極之間的良好導(dǎo)電性,還具有減輕極板彎曲、防止活性物質(zhì)脫落等功能。隨著汽車工業(yè)的飛速發(fā)展,對起動型鉛酸蓄電池的性能要求越來越高,作為鉛酸蓄電池四大組件之一的隔板,其性能的好壞直接影響鉛酸蓄電池質(zhì)量的高低。目前,在閥控式鉛酸蓄電池中普遍使用超細玻璃纖維隔板(AGM),AGM中纖維全部為超細玻璃纖維棉,以濕法抄造成型,然后再經(jīng)過烘干、卷取、裁分切成各種規(guī)格的隔板。濕法成型生產(chǎn)的隔板具有高孔率、低電阻、耐高溫、耐腐蝕、雜質(zhì)含量低的特性。但是這種隔板濕強度低,隔板中的纖維易發(fā)生游離,電解液飽和時沒有氧氣通道,易造成電池失水,電解液濃度上升,腐蝕極板;且在高震動條件下使用,極群壓力下降的較快,如果極板上有鉛渣存在既有可能造成電池短路,造成電池失效。綜上所述,現(xiàn)有技術(shù)中的啟停汽車蓄電池超細玻璃纖維隔板,存在濕強度低,濕態(tài)保壓能力低,以及耐振動性不佳的問題。技術(shù)實現(xiàn)要素:本發(fā)明實施例提供一種啟停汽車蓄電池隔板及其制備方法,用以解決現(xiàn)有技術(shù)中存在啟停汽車蓄電池超細玻璃纖維隔板的濕強度低,濕態(tài)保壓能力低,以及耐振動性不佳的問題。本發(fā)明實施例提供一種啟停汽車蓄電池隔板,包括:隔板原材料包括:玻璃纖維棉和憎水纖維;所述隔板原材料各組分所占的質(zhì)量比例為:玻璃纖維棉85~95%、憎水纖維5~15%;其中,玻璃纖維棉的直徑為0.8~1.5μm,憎水纖維直徑為10~15μm。本發(fā)明實施例提供一種啟停汽車蓄電池隔板的制備方法,包括:將玻璃纖維棉、憎水纖維和分散劑加入到制漿機中,向制漿機中加水將玻璃纖維棉、憎水纖維和分散劑的混合物稀釋為濃度體積百分比為0.75~1.0%的稀釋液,將稀釋液疏解為玻璃纖維棉和憎水纖維均勻分布的原漿料,將原漿料泵入貯漿池中備用;從貯漿池中取出原漿料,加水將原漿料稀釋為濃度百分比為0.1~0.5%的稀釋漿料,通過錐形除渣器對稀釋漿料進行除渣,將除渣后的稀釋漿料輸送至貯漿池備用;從貯漿池中取出除渣后的稀釋漿料,在紙機成型部經(jīng)過自然脫水和機械脫水形成濕隔板;利用熱空氣除去濕隔板中的水分,并使憎水纖維不被熔化掉;將除去水分的濕隔板在卷取機上卷取成半成品卷;將半成品卷裁分為所需規(guī)格的隔板。本發(fā)明實施例中,提供一種啟停汽車蓄電池隔板及其制備方法,該隔板保留了普通AGM隔板孔率高、電阻低、孔徑小等優(yōu)勢,提高了干、濕態(tài)抗張強度、抗穿刺能力、濕態(tài)保壓能力。本發(fā)明的混合纖維蓄電池隔板干、濕態(tài)強度提升30~50%,抗穿刺能力提升了近一倍,濕態(tài)保壓能提升10~20%。附圖說明圖1為本發(fā)明實施例提供的一種啟停汽車蓄電池隔板的制備方法流程圖。具體實施方式下面將結(jié)合本發(fā)明實施例中的附圖,對本發(fā)明實施例中的技術(shù)方案進行清楚、完整地描述,顯然,所描述的實施例僅僅是本發(fā)明一部分實施例,而不是全部的實施例?;诒景l(fā)明中的實施例,本領(lǐng)域普通技術(shù)人員在沒有做出創(chuàng)造性勞動前提下所獲得的所有其他實施例,都屬于本發(fā)明保護的范圍。本發(fā)明實施例提供的一種啟停汽車蓄電池隔板,隔板原材料包括:玻璃纖維棉和憎水纖維;隔板原材料各組分所占的質(zhì)量比例為:玻璃纖維棉85~95%、憎水纖維5~15%;其中,玻璃纖維棉的直徑為0.8~1.5μm,憎水纖維直徑為10~15μm。圖1為本發(fā)明實施例提供的一種啟停汽車蓄電池隔板的制備方法流程圖。如圖1所示,本發(fā)明實施例提供的一種啟停汽車蓄電池隔板的制備方法,包括以下步驟:步驟S101,將玻璃纖維棉、憎水纖維和分散劑加入到制漿機中,向制漿機中加水將玻璃纖維棉、憎水纖維和分散劑的混合物稀釋為濃度體積百分比為0.75~1.0%的稀釋液,將稀釋液疏解為玻璃纖維棉和憎水纖維均勻分布的原漿料,將原漿料泵入貯漿池中備用。需要說明的是,步驟S101為制漿過程,其中,分散劑可選用硫酸。步驟S102,從貯漿池中取出原漿料,加水將原漿料稀釋為濃度百分比為0.1~0.5%的稀釋漿料,通過錐形除渣器對稀釋漿料進行除渣,將除渣后的稀釋漿料輸送至貯漿池備用。需要說明的是,步驟S102為漿料的處理和出渣過程。步驟S103,從貯漿池中取出除渣后的稀釋漿料,在紙機成型部經(jīng)過自然脫水和機械脫水形成濕隔板。需要說明的是,步驟S103為隔板的成型過程。步驟S104,利用熱空氣除去濕隔板中的水分,并使憎水纖維不被熔化掉。需要說明的是,步驟S104為隔板烘干過程。步驟S105,將除去水分的濕隔板在卷取機上卷取成半成品卷。需要說明的是,步驟S105為隔板卷取過程。步驟S106,將半成品卷裁分為所需規(guī)格的隔板。需要說明的是,步驟S106為隔板裁分過程。本發(fā)明主要針對目前沒有用于啟動的免維護閥控鉛酸蓄電池而設(shè)計的,由于AGM隔板在震動條件下濕態(tài)保壓能力下降較快,隔板中纖維發(fā)生游離,造成電池失效。經(jīng)過反復(fù)試驗確定隔板的配方,保留了AGM隔板的孔率高、電阻小的優(yōu)勢,增加了隔板的濕態(tài)保壓能力、增強了隔板的濕強度,從而提升了隔板的耐震動性能,并提升了隔板的抗穿刺性能。混合纖維蓄電池隔板干、濕態(tài)強度提升30~50%,抗穿刺能力提升了近一倍,濕態(tài)保壓能提升10~20%,使混合纖維蓄電池隔板適用于制造閥控免維護起動型鉛酸蓄電池。本發(fā)明啟停汽車蓄電池隔板適用于閥控免維護起動型鉛酸蓄電池,它針對AGM隔板干濕態(tài)強度低、濕態(tài)保壓能力低、耐震性差、抗穿刺能力低等問題進行了組方改進,具體體現(xiàn)如下二個方面:1、加入一定量憎水纖維;2、減小玻璃纖維的直徑,由普通的1.2~2.0μm的直徑玻璃纖維棉,改進為0.8~1.5μm直徑的超細玻璃纖維棉。經(jīng)過上述改進后制成的隔板保留了孔率高、電阻小的優(yōu)點,克服濕態(tài)保壓能力低、濕強度低、耐震性能差、抗穿刺能力差的缺陷,形成一種適用于制造閥控免維護起動型鉛酸蓄電池。表1為本發(fā)明隔板的性能檢測情況。由表1可看出,本發(fā)明隔板的干、濕態(tài)強度大幅提升,電池在使用過程纖維不發(fā)生游離;抗穿刺能力大幅提升,使電池在裝配過程中不會因有鉛渣存在造成電池短路,極板在充放電時會發(fā)生體積變化,對隔板有擠壓力,隔板的抗穿刺能力提升后,也就提高了隔板的抗擠壓能力,提高了電池的壽命;AGM隔板的濕態(tài)保壓能以一般只有65%左右,本發(fā)明隔板濕態(tài)保壓能力超過80%,因而能保證電池在使用過程極板上的活性物質(zhì)不活脫落,提高了電池的使用壽命;AGM隔板裝配的電池耐4g震動只有4小時左右,而使用本發(fā)明的隔板能耐4g震動12小時,大大提高了電池的壽命。表1隔板的性能檢測情況檢測結(jié)果標準備注濕態(tài)強度N/mm20.36≥0.2大幅超出標準干態(tài)強度N/mm20.53≥0.35大幅超出標準抗穿刺能力N/mm7.8>4大大超出標準濕態(tài)保壓能力%84≥60達到標準耐震性能h12≥6大大超出標準孔率%92.8≥90達到標準電阻Ω·dm2/mm0.00029≤0.0005達到標準以上公開的僅為本發(fā)明的幾個具體實施例,本領(lǐng)域的技術(shù)人員可以對本發(fā)明進行各種改動和變型而不脫離本發(fā)明的精神和范圍,倘若本發(fā)明的這些修改和變型屬于本發(fā)明權(quán)利要求及其等同技術(shù)的范圍之內(nèi),則本發(fā)明也意圖包含這些改動和變型在內(nèi)。當前第1頁1 2 3