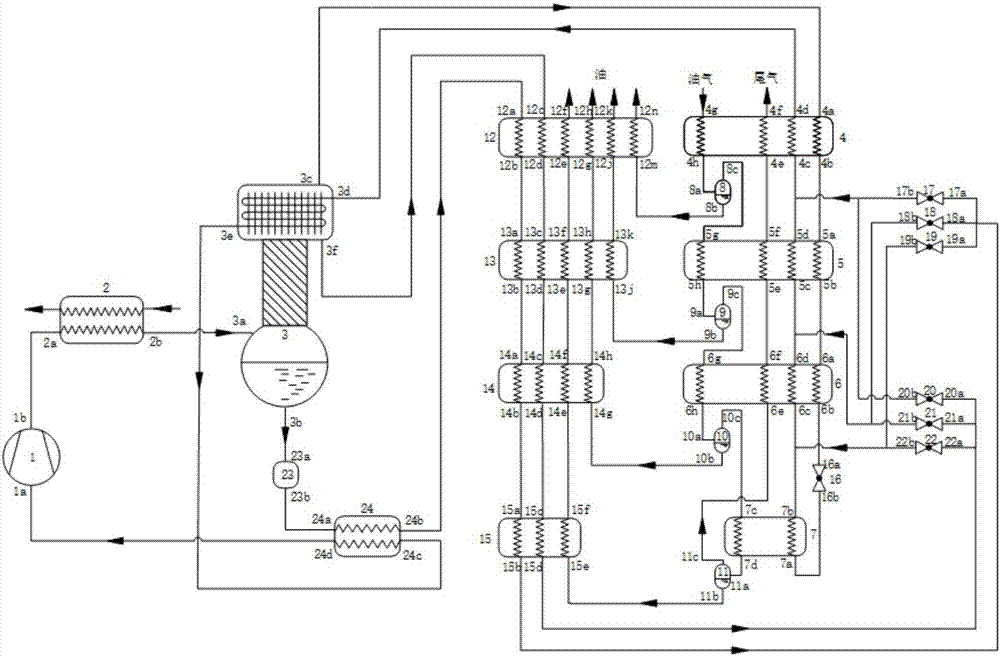
本發(fā)明涉及油氣分離
技術(shù)領(lǐng)域:
,尤其涉及一種帶冷量回收的精餾型自復(fù)疊低溫冷凝油氣分離系統(tǒng)。
背景技術(shù):
:油庫(kù)、加油站、石化加工等場(chǎng)所中儲(chǔ)存的一些油品中含有大量易揮發(fā)的輕烴組分,易在儲(chǔ)運(yùn)過(guò)程中揮發(fā)并且混合在空氣中,造成油品損耗、環(huán)境污染和安全隱患。所以有必要對(duì)這些場(chǎng)所中的含油空氣進(jìn)行處理。國(guó)標(biāo)gb20950-2007《儲(chǔ)油庫(kù)大氣污染物排放標(biāo)準(zhǔn)》和gb20952-2007《加油站大氣污染物排放標(biāo)準(zhǔn)》等規(guī)范中,均明確規(guī)定了排放的油氣中非甲烷總烴含量應(yīng)不大于25g/cm3。在油氣分離領(lǐng)域中,冷凝法由于其可分離出較純凈的產(chǎn)品,適合于較高濃度烴蒸汽的分離回收,受到人們的關(guān)注。最初人們普遍采用復(fù)疊制冷循環(huán)來(lái)逐級(jí)降溫冷凝空氣中的油氣,即采用不同制冷劑運(yùn)行在多個(gè)制冷循環(huán)中獲得不同的溫度位以冷凝不同沸點(diǎn)的烴組分。但是復(fù)疊制冷系統(tǒng)所需設(shè)備較多,逐漸被混合制冷劑制冷循環(huán)而替代。通常,混合制冷劑油氣分離系統(tǒng)中采用了自復(fù)疊制冷循環(huán)的思想,制冷劑的循環(huán)中有多級(jí)氣液分離過(guò)程,以便高低沸點(diǎn)的制冷劑分離更加完全;同時(shí)一般的中小型系統(tǒng)因成本考慮會(huì)使用普通的油潤(rùn)滑壓縮機(jī),多級(jí)分離可將制冷劑帶出的潤(rùn)滑油冷凝下來(lái),避免其進(jìn)入低溫段堵塞節(jié)流裝置。但是分離級(jí)的增多會(huì)導(dǎo)致系統(tǒng)的結(jié)構(gòu)復(fù)雜化,變工況性能變差。特別是對(duì)于小型、微型規(guī)模的油氣分離系統(tǒng),結(jié)構(gòu)簡(jiǎn)單非常重要。目前的油氣分離裝置專利中,較少涉及對(duì)已冷凝的油的進(jìn)一步處理,一般是將冷凝油直接收集起來(lái),浪費(fèi)了不同溫度位冷凝油中的冷量。公告號(hào)為cn102141317a的中國(guó)專利文獻(xiàn)公開(kāi)了一種精餾型自復(fù)疊氣體液化系統(tǒng),包括壓縮機(jī)、冷凝器、精餾裝置以及原料氣液化回路;壓縮機(jī)出料口與冷凝器進(jìn)料口相連,冷凝器的出料口與精餾裝置釜中進(jìn)料口相連,精餾裝置包括精餾塔以及與精餾塔精餾段頂部連通的塔頂換熱器,塔頂換熱器頂部的出料口與原料氣液化回路相連,原料氣穿過(guò)原料氣液化回路得到最終液化產(chǎn)品。該發(fā)明利用精餾裝置代替?zhèn)鹘y(tǒng)混合工質(zhì)氣體液化系統(tǒng)的多級(jí)分離過(guò)程,并利用從精餾裝置底部和頂部引出的不同成分的高壓液體分別減壓進(jìn)入原料氣液化回路中,優(yōu)化匹配原料氣降溫液化過(guò)程中的水當(dāng)量變化,來(lái)逐段冷卻原料氣,具有結(jié)構(gòu)簡(jiǎn)單、運(yùn)行可靠和系統(tǒng)液化效率高等優(yōu)點(diǎn),特別適用于各種小型和微型氣體液化系統(tǒng)。然而,該裝置適用范圍有限,只適用于需要將原料氣全部液化的場(chǎng)合。而在處理含油空氣的場(chǎng)合中,只需要將油盡可能冷凝液化下來(lái),而空氣是不被液化的,所以該裝置不適用于油氣分離領(lǐng)域。同時(shí),經(jīng)冷凝的不同低溫位的油以及除去油的低溫空氣中均含大量冷量,值得充分利用。技術(shù)實(shí)現(xiàn)要素:針對(duì)現(xiàn)有技術(shù)存在的不足,本發(fā)明提供了一種帶冷量回收的精餾型自復(fù)疊低溫冷凝油氣分離系統(tǒng),該系統(tǒng)將制冷劑循環(huán)中的多級(jí)分離過(guò)程合并為一個(gè)精餾過(guò)程,運(yùn)行可靠,用一套普通的油潤(rùn)滑壓縮機(jī)就能完成分離尾氣中的烴組分,使排放物濃度滿足國(guó)標(biāo)要求,特別適合油庫(kù)、加油站等場(chǎng)所的揮發(fā)性油氣的處理。本發(fā)明的技術(shù)方案如下:一種帶冷量回收的精餾型自復(fù)疊低溫冷凝油氣分離系統(tǒng),包括壓縮機(jī)、冷凝器、精餾裝置以及油氣冷凝分離及冷量回收回路;所述的壓縮機(jī)出口與冷凝器進(jìn)口相連;所述的冷凝器出口與精餾裝置進(jìn)口相連;所述的精餾裝置包括精餾柱以及與精餾柱頂部相連的柱頂換熱器,柱頂換熱器頂部出口與油氣冷凝分離及冷量回收回路相連,所述的油氣冷凝分離及冷量回收回路包括第一換熱器單元、第二換熱器單元、第三換熱器單元、第一節(jié)流元件(16)和分離器單元;所述的第一換熱器單元包括第一換熱器(4)、第二換熱器(5)和第三換熱器(6)中的一者或幾者的組合;所述的第二換熱器單元包括蒸發(fā)器(7);所述的第三換熱器單元包括第四換熱器(12)、第五換熱器(13)、第六換熱器(14)和第七換熱器(15)中的一者或幾者的組合;第一節(jié)流元件(16)設(shè)置于第一換熱器單元和第二換熱器單元之間;分離器單元包括第一分離器(8)、第二分離器(9)、第三分離器(10)和第四分離器(11)中的一者或幾者的組合;所述的第一換熱器單元的各換熱器內(nèi)均設(shè)有一個(gè)正流制冷劑管道、一個(gè)返流制冷劑管道、一個(gè)油氣管道和一個(gè)尾氣管道;所述的蒸發(fā)器內(nèi)設(shè)有一個(gè)低壓制冷劑管道和一個(gè)油氣管道;所述的精餾裝置的柱頂換熱器內(nèi)設(shè)有冷卻管道;所述的第三換熱器單元的各換熱器內(nèi)均設(shè)有釜底液管道、回流液管道和多個(gè)冷凝油管道;具體地,第四換熱器內(nèi)設(shè)有四個(gè)冷凝油管道,第五換熱器內(nèi)設(shè)有三個(gè)冷凝油管道,第六換熱器內(nèi)設(shè)有兩個(gè)冷凝油管道,第七換熱器內(nèi)設(shè)有一個(gè)冷凝油管道;所述的第一分離器、第二分離器、第三分離器和第四分離器均設(shè)有氣相出口和液相出口;所述的柱頂換熱器頂部出口與第一換熱器的正流制冷劑管道進(jìn)口相連;所述第一換熱器的正流制冷劑管道出口與第二換熱器的正流制冷劑管道進(jìn)口相連;所述第二換熱器的正流制冷劑管道出口與第三換熱器的正流制冷劑管道進(jìn)口相連;所述第一節(jié)流裝置的進(jìn)口與第三換熱器的正流制冷劑管道出口相連,出口與蒸發(fā)器的低壓制冷劑管道進(jìn)口相連;所述蒸發(fā)器的低壓制冷劑管道出口與第三換熱器的返流制冷劑管道進(jìn)口相連;所述第三換熱器的返流制冷劑管道出口與第二換熱器的返流制冷劑管道進(jìn)口相連;所述第二換熱器的返流制冷劑管道出口與第一換熱器的返流制冷劑管道進(jìn)口相連;所述第一換熱器的返流制冷劑管道出口與精餾裝置的柱頂換熱器冷卻管道的進(jìn)口相連;所述柱頂換熱器冷卻管道的出口與壓縮機(jī)的吸氣口相連;所述精餾裝置的底部出口與第四換熱器的釜底液管道進(jìn)口相連;所述第四換熱器的釜底液管道出口與第五換熱器的釜底液管道進(jìn)口相連;所述第五換熱器的釜底液管道出口與第六換熱器的釜底液管道進(jìn)口相連;所述第六換熱器的釜底液管道出口與第七換熱器的釜底液管道進(jìn)口相連;所述的精餾裝置的柱頂換熱器的底部出口與第四換熱器的回流液管道進(jìn)口相連;所述第四換熱器的回流液管道出口與第五換熱器的回流液管道進(jìn)口相連;所述第五換熱器的回流液管道出口與第六換熱器的回流液管道進(jìn)口相連;所述第六換熱器的回流液管道出口與第七換熱器的回流液管道進(jìn)口相連;所述第七換熱器的釜底液管道出口和回流液管道出口均通過(guò)三條支路管道分別與第一換熱器、第二換熱器、第三換熱器的返流制冷劑管道的進(jìn)口相連;所述的支路管道上均設(shè)有一個(gè)節(jié)流元件;所述各換熱器的返流制冷劑管道的連接方式是為了實(shí)現(xiàn)對(duì)正流制冷劑管道內(nèi)制冷劑以及待處理油氣的冷卻;第一換熱器返流制冷劑管道出口與柱頂換熱器的冷卻管道進(jìn)口相連,柱頂換熱器的冷卻管道出口與壓縮機(jī)吸氣口相連,以實(shí)現(xiàn)制冷劑的循環(huán)制冷。在所述的油氣冷凝及冷量回收回路中,油氣首先進(jìn)入第一換熱器的油氣管道進(jìn)口,第一換熱器的油氣管道出口與第一分離器的進(jìn)口相連;經(jīng)過(guò)第一分離器的氣液分離過(guò)程,第一分離器的氣相出口與第二換熱器的油氣管道進(jìn)口相連;第二換熱器的油氣管道出口與第二分離器的進(jìn)口相連;經(jīng)過(guò)第二分離器的氣液分離過(guò)程,第二分離器的氣相出口與第三換熱器的油氣管道進(jìn)口相連;第三換熱器的油氣管道出口與第三分離器的進(jìn)口相連;經(jīng)過(guò)第三分離器的氣液分離過(guò)程,第三分離器的氣相出口與蒸發(fā)器的油氣管道進(jìn)口相連;蒸發(fā)器的油氣管道出口與第四分離器的進(jìn)口相連;經(jīng)過(guò)第四分離器的氣液分離過(guò)程,氣相部分即為符合排放濃度要求的低溫尾氣。該低溫尾氣經(jīng)第四分離器的氣相出口進(jìn)入第三換熱器的尾氣管道進(jìn)口,第三換熱器尾氣管道出口與第二換熱器的尾氣管道進(jìn)口相連;第二換熱器尾氣管道出口與第一換熱器的尾氣管道進(jìn)口相連,最終尾氣經(jīng)第一換熱器尾氣管道出口排放;經(jīng)過(guò)逐步冷凝并分離出來(lái)的冷凝油液體經(jīng)第一分離器的液相出口、第二分離器的液相出口、第三分離器的液相出口、第四分離器的液相出口排出。各分離器排出的不同溫度的冷凝油將穿過(guò)第三換熱器單元內(nèi)的各換熱器回收冷量,溫度越低的冷凝油經(jīng)過(guò)的換熱器越多。具體地,第一分離器液相出口與第四換熱器的第一冷凝油管道進(jìn)口相連,冷凝油經(jīng)過(guò)第四換熱器升溫后從第四換熱器的一號(hào)冷凝油管道出口排出;第二分離器液相出口與第五換熱器的第一冷凝油管道進(jìn)口相連;第五換熱器的第一冷凝油管道出口與第四換熱器的第二冷凝油管道進(jìn)口相連,冷凝油經(jīng)過(guò)第五換熱器和第四換熱器升溫后從第四換熱器的第二冷凝油管道出口排出;第三分離器液相出口與第六換熱器的第一冷凝油管道進(jìn)口相連;第六換熱器的第一冷凝油管道出口與第五換熱器的第二冷凝油管道進(jìn)口相連;第五換熱器的第二冷凝油管道出口與第四換熱器的第三冷凝油管道進(jìn)口相連,冷凝油經(jīng)過(guò)第六換熱器、第五換熱器和第四換熱器升溫后從第四換熱器的第三冷凝油管道出口排出;第四分離器液相出口與第七換熱器的第一冷凝油管道進(jìn)口相連;第七換熱器的第一冷凝油管道出口與第六換熱器的第二冷凝油管道進(jìn)口相連;第六換熱器的第二冷凝油管道出口與第五換熱器的第三冷凝油管道進(jìn)口相連;第五換熱器的第三冷凝油管道出口與第四換熱器的第四冷凝油管道進(jìn)口相連,冷凝油經(jīng)過(guò)第七換熱器、第六換熱器、第五換熱器和第四換熱器升溫后從第四換熱器的第四冷凝油管道出口排出。從第四換熱器的第一、第二、第三、第四冷凝油管道出口的復(fù)溫后的冷凝油可以分別或混合后回收至儲(chǔ)罐,或者以其他方式加以儲(chǔ)存和利用。本發(fā)明中,第一換熱器單元并不局限于由三個(gè)換熱器構(gòu)成,可以根據(jù)實(shí)際情況調(diào)整第一換熱器單元內(nèi)換熱器的個(gè)數(shù);同樣地,第三換熱器單元也并不局限于由四個(gè)換熱器構(gòu)成,可以根據(jù)油氣分離的級(jí)數(shù)和實(shí)際情況來(lái)調(diào)整第三換熱器單元內(nèi)換熱器的個(gè)數(shù)。隨著第一換熱器單元內(nèi)換熱器個(gè)數(shù)的調(diào)整,分離器單元內(nèi)分離器的數(shù)目要作相應(yīng)的調(diào)整,第三換熱器單元內(nèi)各換熱器的冷凝油管道數(shù)目應(yīng)做相應(yīng)的調(diào)整,第七換熱器的釜底液管道出口和回流液管道出口連接的支路管道數(shù)目及支路上的節(jié)流元件的數(shù)目也作相應(yīng)的調(diào)整;本發(fā)明將需要處理的油氣依次通入油氣冷凝分離及冷量回收回路的換熱器單元內(nèi),由返流的低壓制冷劑提供主要的冷量,并且按照要處理的油氣成分特點(diǎn),利用精餾裝置底部和頂部不同成分的高壓制冷劑液體分別節(jié)流后與低壓制冷劑混合,以優(yōu)化和匹配油氣降溫過(guò)程中的水當(dāng)量變化,逐段冷卻油氣,減小不同溫度段換熱器內(nèi)混合制冷劑與油氣之間的傳熱溫差,從而適應(yīng)不同成分油氣的冷凝分離和減小系統(tǒng)的單位耗功。被逐級(jí)冷卻的油氣經(jīng)過(guò)多次氣液分離,最終形成了符合排放濃度要求的低溫尾氣,可以再提供一部分冷量,復(fù)溫后排放;不同溫度下冷凝出來(lái)的冷凝油液體用于預(yù)冷精餾裝置底部和頂部引出的高壓制冷劑液體,使之降低一定溫度后再節(jié)流與低壓制冷劑混合,實(shí)現(xiàn)了冷凝油的冷量回收,更有利于能量的綜合利用。為保證整個(gè)油氣分離系統(tǒng)的穩(wěn)定性,同時(shí)實(shí)現(xiàn)能源的綜合利用,在優(yōu)選的技術(shù)方案中,可以在所述的精餾裝置底部的液體出口管道上設(shè)置一個(gè)或多個(gè)干燥過(guò)濾器,實(shí)現(xiàn)對(duì)底部流出液體的干燥和過(guò)濾;同時(shí)還可以設(shè)置一個(gè)或多個(gè)釜底換熱器,對(duì)底部流出的制冷劑進(jìn)行預(yù)冷后,再讓其被冷凝油進(jìn)一步預(yù)冷。當(dāng)干燥過(guò)濾器和釜底換熱器的個(gè)數(shù)均為一個(gè)時(shí),所述的精餾裝置的底部出口首先依次連接干燥過(guò)濾器和釜底換熱器,再與第四換熱器的釜底液管道進(jìn)口相連;所述的釜底換熱器內(nèi)設(shè)有高壓制冷劑管道和低壓制冷劑管道;所述的干燥過(guò)濾器進(jìn)口與精餾裝置底部出口相連,出口與釜底換熱器的高壓制冷劑管道進(jìn)口相連;所述釜底換熱器的高壓制冷劑管道出口與第四換熱器的釜底液管道進(jìn)口相連;所述釜底換熱器的低壓制冷劑管道進(jìn)口與精餾裝置的柱頂換熱器出口相連,出口與壓縮機(jī)吸氣口相連。利用低壓制冷劑對(duì)精餾裝置底部的液體制冷劑進(jìn)行預(yù)冷,實(shí)現(xiàn)能量的綜合利用;所述的釜底換熱器內(nèi)的高壓制冷劑管道和低壓制冷劑管道的進(jìn)口分別位于該換熱器的兩側(cè),以實(shí)現(xiàn)逆流換熱。若待處理的油氣中含水量較高,或者是待處理的油氣在冷凝處理之前沒(méi)有經(jīng)過(guò)其他干燥處理,在另一種優(yōu)選的技術(shù)方案中,可以將返流經(jīng)過(guò)第一換熱器單元的仍處于-10℃~-20℃的尾氣與進(jìn)入第一換熱器單元之前的待處理油氣在第四換熱器單元中進(jìn)行回?zé)?。所述的第四換熱器單元包括第八換熱器、第九換熱器、第一截止閥、第二截止閥、第三截止閥、第四截止閥、第五截止閥、第六截止閥、第七截止閥、第八截止閥;所述第八換熱器和第九換熱器并聯(lián)設(shè)置;所述的第八換熱器和第九換熱器內(nèi)部均有一個(gè)油氣管道和一個(gè)尾氣管道;所述第一換熱器的尾氣管道出口分別與第五截止閥和第七截止閥進(jìn)口相連,使得尾氣分為兩條支路;所述第八換熱器的油氣管道進(jìn)口與第一截止閥的出口相連,油氣管道出口與第二截止閥的進(jìn)口相連,尾氣管道進(jìn)口和第五截止閥的出口相連,尾氣管道出口與第六截止閥的進(jìn)口相連;所述的第九換熱器的油氣管道進(jìn)口與第三截止閥的出口相連,油氣管道出口與第四截止閥的進(jìn)口相連,尾氣管道進(jìn)口與第七截止閥的出口相連,尾氣管道出口與第八截止閥的進(jìn)口相連;所述第二截止閥的出口和第四截止閥的出口相連,匯聚成一個(gè)管道后與第一換熱器的油氣管道進(jìn)口相連;所述第六截止閥的出口和第八截止閥的出口相連,匯聚成一個(gè)管道后作為尾氣的出口。所述的第八換熱器和第九換熱器的油氣管道和尾氣管道的進(jìn)口均位于各自換熱器的兩側(cè),以實(shí)現(xiàn)逆流換熱。在第四換熱器單元中,利用尾氣的剩余冷量為油氣提供預(yù)冷,使得油氣中的大部分水分在0~4℃凝結(jié),實(shí)現(xiàn)能量的綜合利用;并采用兩換熱器切換運(yùn)行的模式,使一個(gè)換熱器運(yùn)行時(shí),另一個(gè)換熱器排水或除霜,增加裝置連續(xù)運(yùn)行的穩(wěn)定性。若待處理的油氣中含低沸點(diǎn)組分較多時(shí),要將其處理到可排放的濃度標(biāo)準(zhǔn),所需的制冷溫度也要求更低,制冷劑回路中需采用低沸點(diǎn)組分濃度較高的多元混合制冷劑。這將導(dǎo)致油氣分離系統(tǒng)中制冷劑回路的壓縮機(jī)在開(kāi)始降溫階段的壓比和排氣溫度過(guò)高,大大降低壓縮機(jī)壽命,甚至導(dǎo)致壓縮機(jī)因壓力保護(hù)而不能開(kāi)啟,使整個(gè)油氣分離系統(tǒng)不能正常運(yùn)行,冷卻效率低。為解決這些問(wèn)題,在另一種優(yōu)選的技術(shù)方案中,可以在所述的精餾裝置與壓縮機(jī)吸氣口之間設(shè)置并聯(lián)的第一變濃度回路和第二變濃度回路。第一變濃度回路包括依次串聯(lián)的第九截止閥、儲(chǔ)液罐和第十截止閥;第二變濃度回路包括依次串聯(lián)的第十一截止閥、第一儲(chǔ)氣罐和第十二截止閥;所述第九截止閥的進(jìn)口與精餾裝置的底部出口相連,所述第十一截止閥的進(jìn)口與精餾裝置的柱頂換熱器頂部出口相連,所述第十截止閥的出口和第十二截止閥的出口均與壓縮機(jī)吸氣口相連。通過(guò)第一變濃度回路以及第二變濃度回路在不同過(guò)程的啟用和停用,來(lái)調(diào)節(jié)參與循環(huán)的混合制冷劑中低沸點(diǎn)組分的濃度,可以改善開(kāi)機(jī)過(guò)程,或是達(dá)到更低的制冷溫度。為進(jìn)一步便于調(diào)節(jié)制冷劑回路中低沸點(diǎn)制冷劑的含量,可以在所述第一節(jié)流元件的進(jìn)口和所述第三換熱器的正流制冷劑管道出口之間設(shè)有第五分離器;所述的第五分離器和壓縮機(jī)的吸氣口之間設(shè)有第三變濃度回路;所述的第三變濃度回路包括依次串聯(lián)的第十三截止閥、第二儲(chǔ)氣罐和第十四截止閥,第十三截止閥的進(jìn)口與第五分離器的氣相出口相連。所述的冷凝器、第一換熱器、第二換熱器、第三換熱器、蒸發(fā)器、第四換熱器、第五換熱器、第六換熱器、第七換熱器、釜底換熱器、第八換熱器和第九換熱器可選用常見(jiàn)的套管式換熱器、噴淋式換熱器、殼管式換熱器或者板翅式換熱器。根據(jù)實(shí)際需要連接的管路和具體場(chǎng)合選擇不同類型的換熱器。本發(fā)明中優(yōu)選板翅式換熱器。所述的油氣分離系統(tǒng)內(nèi)采用的制冷劑為二元或二元以上的非共沸混合工質(zhì),常見(jiàn)的組分主要有:氮?dú)?、惰性氣體、烴類、烴的鹵化物、二氧化碳等。所述的各節(jié)流元件為手動(dòng)節(jié)流閥、自動(dòng)節(jié)流閥或毛細(xì)管,以起到節(jié)流降溫的作用。所述的精餾裝置中的精餾柱為填料式或塔板式。所述的各截止閥為手動(dòng)或者自動(dòng)的雙向截止閥,以實(shí)現(xiàn)截止閥的自動(dòng)或手動(dòng)控制,其中第一截止閥與第二截止閥聯(lián)動(dòng),第三截止閥與第四截止閥聯(lián)動(dòng),第五截止閥與第六截止閥聯(lián)動(dòng),第七截止閥與第八截止閥聯(lián)動(dòng)。與現(xiàn)有技術(shù)相比,本發(fā)明的有益效果為:(1)本發(fā)明的制冷系統(tǒng)的結(jié)構(gòu)簡(jiǎn)化,運(yùn)行可靠。對(duì)于含低沸點(diǎn)成分較多的油氣,所需的最低制冷溫度較低,如-110℃~-130℃。要達(dá)到如此低的制冷溫度,傳統(tǒng)的混合制冷劑自復(fù)疊制冷系統(tǒng)一般需要2~5級(jí)分離過(guò)程。本發(fā)明采用精餾裝置來(lái)代替多級(jí)分離過(guò)程,可以使得系統(tǒng)結(jié)構(gòu)大大簡(jiǎn)化,并且使得進(jìn)入到低溫段的制冷劑中攜帶的潤(rùn)滑油被有效去除,保證了系統(tǒng)的可靠運(yùn)行。(2)本發(fā)明可提高油氣冷凝分離系統(tǒng)的熱力學(xué)效率。針對(duì)不同成分的油氣,根據(jù)其降溫過(guò)程中的水當(dāng)量分布特點(diǎn)和流量不同,可以調(diào)節(jié)精餾裝置底部、頂部?jī)商幰龅牟煌煞值母邏夯旌现评鋭┑牧髁恳约盎旌衔恢茫詢?yōu)化換熱器內(nèi)的溫度分布,減小傳熱溫差,從而提高系統(tǒng)的熱力學(xué)效率,減小系統(tǒng)耗功。(3)本發(fā)明充分利用尾氣的余冷。若油氣中含水量多或者在進(jìn)行冷凝處理前沒(méi)有進(jìn)行過(guò)干燥,則可以利用尾氣中的余冷對(duì)油氣進(jìn)行預(yù)冷,使得大部分水冷凝下來(lái),減小在后續(xù)低溫段結(jié)霜的可能性。同時(shí)預(yù)冷換熱器單元采用切換運(yùn)行的方式,增加裝置的連續(xù)運(yùn)行穩(wěn)定性。(4)本發(fā)明有效回收了冷凝下來(lái)的油品的冷量。目前較少發(fā)明涉及到冷凝油的冷量利用,所以本發(fā)明針對(duì)這一點(diǎn),將不同溫度的低溫冷凝油用于逐步降低精餾裝置釜底液體制冷劑的預(yù)冷,充分利用了冷凝油的冷量,同時(shí)降低釜底液體制冷劑的溫度,有利于其對(duì)高壓制冷劑的預(yù)冷。體現(xiàn)了能量的綜合利用,進(jìn)一步降低系統(tǒng)的耗功。(5)本發(fā)明能優(yōu)化油氣分離系統(tǒng)的開(kāi)始降溫階段,提高降溫速率。開(kāi)始降溫階段內(nèi),混合制冷劑中高沸點(diǎn)組分濃度增加能降低系統(tǒng)的開(kāi)機(jī)壓力,改善該階段內(nèi)壓縮機(jī)排氣溫度過(guò)高和壓比偏大的問(wèn)題,改善系統(tǒng)的動(dòng)態(tài)運(yùn)行特性。(6)本發(fā)明能優(yōu)化油氣分離系統(tǒng)的最終降溫階段,使得系統(tǒng)達(dá)到更低的制冷溫度,提高系統(tǒng)的熱力學(xué)效率。降溫最終階段內(nèi),混合制冷劑中低沸點(diǎn)組分濃度增加能改善換熱器中高低壓側(cè)混合制冷劑的水當(dāng)量匹配。從而降低系統(tǒng)能達(dá)到的最低溫度,提高系統(tǒng)的熱力學(xué)性能。(7)本發(fā)明三個(gè)變濃度回路均結(jié)構(gòu)簡(jiǎn)單,調(diào)節(jié)能力強(qiáng),操作方便。在系統(tǒng)設(shè)計(jì)時(shí)就可以根據(jù)所需要實(shí)現(xiàn)的最低制冷溫度設(shè)置若干個(gè)變濃度回路,也可以在系統(tǒng)運(yùn)行時(shí)根據(jù)需要啟用若干個(gè)變濃度回路。附圖說(shuō)明圖1為本發(fā)明精餾型自復(fù)疊低溫冷凝油氣分離系統(tǒng)的第一種實(shí)施方式的結(jié)構(gòu)示意圖;圖2為本發(fā)明精餾型自復(fù)疊低溫冷凝油氣分離系統(tǒng)的第二種實(shí)施方式的結(jié)構(gòu)示意圖;圖3為本發(fā)明精餾型自復(fù)疊低溫冷凝油氣分離系統(tǒng)的第三種實(shí)施方式的結(jié)構(gòu)示意圖;圖4為本發(fā)明精餾型自復(fù)疊低溫冷凝油氣分離系統(tǒng)的第四種實(shí)施方式的結(jié)構(gòu)示意圖;圖5為本發(fā)明精餾型自復(fù)疊低溫冷凝油氣分離系統(tǒng)的第五種實(shí)施方式的結(jié)構(gòu)示意圖。具體實(shí)施方式下面結(jié)合附圖和具體實(shí)施方式對(duì)本發(fā)明一種帶冷量回收的精餾型自復(fù)疊低溫冷凝油氣分離系統(tǒng)作進(jìn)一步詳細(xì)說(shuō)明。實(shí)施例1如圖1所示,一種帶冷量回收的精餾型自復(fù)疊低溫冷凝油氣分離系統(tǒng),包括壓縮機(jī)1、冷凝器2、精餾裝置3、第一換熱器4、第二換熱器5、第三換熱器6、蒸發(fā)器7、第四換熱器12、第五換熱器13、第六換熱器14、第七換熱器15、第一分離器8、第二分離器9、第三分離器10、第四分離器11、第一節(jié)流元件16、第二節(jié)流元件17、第三節(jié)流元件18、第四節(jié)流元件19、第五節(jié)流元件20、第六節(jié)流元件21和第七節(jié)流元件22。精餾裝置3中包括精餾柱以及與精餾柱頂部相連的柱頂換熱器,柱頂換熱器內(nèi)設(shè)有冷卻管道。第一換熱器4、第二換熱器5和第三換熱器6中均設(shè)有一個(gè)正流制冷劑管道、一個(gè)返流制冷劑管道、一個(gè)油氣管道和一個(gè)尾氣管道,外壁上均設(shè)有與管道連通的進(jìn)口或出口,蒸發(fā)器7中設(shè)有一個(gè)低壓制冷劑管道和一個(gè)油氣管道,外壁上設(shè)有與管道連通的進(jìn)口或出口。第四換熱器12、第五換熱器13、第六換熱器14和第七換熱器15中均設(shè)有釜底液管道、回流液管道和多個(gè)冷凝油管道,外壁上均設(shè)有與管道連通的進(jìn)口或出口;具體地,第四換熱器12中有四個(gè)油氣管道(第一、第二、第三、第四),第五換熱器13中有三個(gè)油氣管道(第一、第二、第三),第六換熱器14中有兩個(gè)油氣管道(第一、第二),第七換熱器15中有一個(gè)油氣管道(第一)。壓縮機(jī)1的出口1b與冷凝器2的制冷劑進(jìn)口2a相連,冷凝器2的制冷劑出口2b與精餾裝置3中精餾柱的中部進(jìn)料口3a相連,精餾柱3的精餾柱底部出液口3b與第四換熱器12的釜底液管道進(jìn)口12a相連;精餾裝置3的柱頂換熱器底部回流液出口3f與第四換熱器12的回流液管道進(jìn)口12c相連;精餾裝置3的柱頂換熱器頂部出口3c與第一換熱器4的高壓制冷劑管道進(jìn)口4a相連。第一換熱器4的正流制冷劑管道出口4b與第二換熱器5的正流制冷劑管道進(jìn)口5a相連;第一換熱器4的返流制冷劑管道進(jìn)口4c與第二換熱器5的返流制冷劑管道出口5d相連,返流制冷劑管道出口4d則與精餾裝置3柱頂換熱器內(nèi)的冷卻管道進(jìn)口3d相連;第一換熱器4中的油氣管道進(jìn)口為4g,尾氣管道出口為4f;第一換熱器4中的油氣管道出口4h與第一分離器8的進(jìn)口8a相連,尾氣管道進(jìn)口4e與第二換熱器5的尾氣管道出口5f相連。第一換熱器4中的正流制冷劑管道進(jìn)口4a、返流制冷劑管道出口4d、尾氣管道出口4f、油氣管道進(jìn)口4g在同一側(cè),而正流制冷劑管道出口4b、返流制冷劑管道進(jìn)口4c、油氣管道出口4h、尾氣管道進(jìn)口4e在另一側(cè),以實(shí)現(xiàn)冷熱流體的逆向換熱。第二換熱器5的正流制冷劑管道出口5b與第三換熱器6的正流制冷劑管道進(jìn)口6a相連,返流制冷劑管道進(jìn)口5c和第三換熱器6的返流制冷劑管道出口6d相連;第二換熱器5的尾氣管道進(jìn)口5e與第三換熱器6的尾氣管道出口6f相連,油氣管道進(jìn)口5g與第一分離器8的氣相出口8c相連,油氣管道出口5h與第二分離器9的進(jìn)口9a相連。第二換熱器5中正流制冷劑管道進(jìn)口5a、返流制冷劑管道出口5d、尾氣管道出口5f、油氣管道進(jìn)口5g在同一側(cè),而正流制冷劑管道出口5b、返流制冷劑管道進(jìn)口5c、尾氣管道進(jìn)口5e、油氣管道出口5h在另一側(cè),以實(shí)現(xiàn)冷熱流體的逆向換熱。第三換熱器6的正流制冷劑管道出口6b與第一節(jié)流元件16的進(jìn)口16a相連,第一節(jié)流元件的出口16b則與蒸發(fā)器7的低壓制冷劑管道進(jìn)口7a相連;第三換熱器6的返流制冷劑管道進(jìn)口6c與蒸發(fā)器7的返流制冷劑管道出口7b相連;第三換熱器6的尾氣管道進(jìn)口6e與第四分離器11的氣相出口11c相連,油氣管道進(jìn)口6g與第二分離器9的氣相出口9c相連,油氣管道出口6h與第三分離器10的進(jìn)口10a相連。第三換熱器6中正流制冷劑管道進(jìn)口6a、返流制冷劑管道出口6d、尾氣管道出口6f、油氣管道進(jìn)口6g在同一側(cè),而正流制冷劑管道出口6b、返流制冷劑管道進(jìn)口6c、尾氣管道進(jìn)口6e、油氣管道出口6h在另一側(cè),以實(shí)現(xiàn)冷熱流體的逆向換熱。蒸發(fā)器7的尾氣管道進(jìn)口7c與第三分離器10的氣相出口10c相連,尾氣管道出口7d與第四分離器11的進(jìn)口11a相連;蒸發(fā)器7中低壓制冷劑管道的出口7b和尾氣管道進(jìn)口7c在同一側(cè),蒸發(fā)器7中低壓制冷劑管道的進(jìn)口7a和尾氣管道出口7d在另一側(cè),以實(shí)現(xiàn)冷熱流體的逆向換熱。第四換熱器12的釜底液管道出口12b與第五換熱器13的釜底液管道進(jìn)口13a相連,回流液管道出口12d與第五換熱器13的回流液管道進(jìn)口13c相連;第四換熱器12的第一冷凝油管道出口為12n,第一冷凝油管道進(jìn)口12m與第一分離器8的液相出口8b相連;第四換熱器12的第二冷凝油管道出口為12k,第二冷凝油管道進(jìn)口12j與第五換熱器13的第一冷凝油管道出口13k相連;第四換熱器12的第三冷凝油管道出口為12h,第三冷凝油管道進(jìn)口12g與第五換熱器13的第二冷凝油管道出口13h相連;第四換熱器12的第四冷凝油管道出口為12f,第四冷凝油管道進(jìn)12e與第五換熱器13的第三冷凝油管道出口13f相連;第四換熱器12中的釜底液管道進(jìn)口12a、回流液管道進(jìn)口12c、第一冷凝油管道出口12n、第二冷凝油管道出口12k、第三冷凝油管道出口12h、第四冷凝油管道12f在同一側(cè),而釜底液管道出口12b、回流液管道出口12d、第一冷凝油管道進(jìn)口12m、第二冷凝油管道進(jìn)口12j、第三冷凝油管道進(jìn)口12g、第四冷凝油管道進(jìn)口12e在另一側(cè),以實(shí)現(xiàn)冷熱流體的逆向換熱。第五換熱器13的釜底液管道出口13b與第六換熱器14的釜底液管道進(jìn)口14a相連,回流液管道出口13d與第六換熱器14的回流液管道進(jìn)口14c相連;第五換熱器13的第一冷凝油管道的進(jìn)口13j與第二分離器9的液相出口9b相連,第二冷凝油管道的進(jìn)口13g與第六換熱器14的第一冷凝油管道出口14h相連,第三冷凝油管道的進(jìn)口13e與第六換熱器14的第二冷凝油管道出口14f相連;第五換熱器13中的釜底液管道進(jìn)口13a、回流液管道進(jìn)口13c、第一冷凝油管道出口13k、第二冷凝油管道出口13h、第三冷凝油管道出口13f在同一側(cè),而釜底液管道出口13b、回流液管道出口13d、第一冷凝油管道進(jìn)口13j、第二冷凝油管道進(jìn)口13g、第三冷凝油管道進(jìn)口13e在另一側(cè),以實(shí)現(xiàn)冷熱流體的逆向換熱。第六換熱器14的釜底液管道出口14b與第七換熱器15的釜底液管道進(jìn)口15a相連,回流液管道出口14d與第七換熱器15的回流液管道進(jìn)口15c相連;第六換熱器14的第一冷凝油管道進(jìn)口14g與第三分離器10的液相出口10b相連,第二冷凝油管道進(jìn)口14e與第七換熱器15的第一冷凝油管道出口15f相連;第六換熱器14中的釜底液管道進(jìn)口14a、回流液管道進(jìn)口14c、第一冷凝油管道的出口14h、第二冷凝油管道出口14f在同一側(cè),而釜底液管道出口14b、回流液管道出口14d、第一冷凝油管道進(jìn)口14g、第二冷凝油管道進(jìn)口14e在另一側(cè),以實(shí)現(xiàn)冷熱流體的逆向換熱。第七換熱器15的釜底液管道出口15b通過(guò)三條支路分別與第二節(jié)流元件17的進(jìn)口17a、第三節(jié)流元件18的進(jìn)口18a、第四節(jié)流元件19的進(jìn)口19a相連;第七換熱器15的回流液管道出口15d通過(guò)另三條支路分別與第五節(jié)流元件20的進(jìn)口20a、第六節(jié)流元件21的進(jìn)口21a、第七節(jié)流元件22的進(jìn)口22a相連;第七換熱器15的第一冷凝油管道進(jìn)口15e與第四分離器11的液相出口11b相連;第七換熱器15中的釜底液管道進(jìn)口15a、回流液管道進(jìn)口15c、第一冷凝油管道出口15f在同一側(cè),而釜底液管道出口15b、回流液管道出口15d、第一冷凝油管道進(jìn)口15e在另一側(cè),以實(shí)現(xiàn)冷熱流體的逆向換熱。第二節(jié)流元件17的出口17b、第五節(jié)流元件20的出口20b均與第一換熱器4的低壓制冷劑管道進(jìn)口4c相連,或與第二換熱器5的低壓制冷劑管道出口5d相連;第三節(jié)流元件18的出口18b、第六節(jié)流元件21的出口21b均與第二換熱器5的低壓制冷劑管道進(jìn)口5c相連,或與第三換熱器6的低壓制冷劑管道出口6d相連;第四節(jié)流元件19的出口19b、第七節(jié)流元件22的出口22b均與第三換熱器6的低壓制冷劑管道進(jìn)口6c相連,或與蒸發(fā)器7的低壓制冷劑管道出口7b相連。上述實(shí)施方式中的冷凝器2、精餾裝置3的柱頂換熱器、第一換熱器4、第二換熱器5、第三換熱器6、蒸發(fā)器7、第四換熱器12、第五換熱器13、第六換熱器14和第七換熱器15為板翅式換熱器。上述實(shí)施方式中的第一節(jié)流元件16、第二節(jié)流元件17、第三節(jié)流元件18、第四節(jié)流元件19、第五節(jié)流元件20、第六節(jié)流元件21和第七節(jié)流元件22為手動(dòng)節(jié)流閥,也可選用常見(jiàn)的自動(dòng)節(jié)流閥或毛細(xì)管,以起到節(jié)流降溫的作用。上述實(shí)施方式中的精餾裝置3與普通制冷裝置中的精餾裝置類似,精餾柱選用常規(guī)的塔板式精餾柱或者填料式精餾柱。上述的各個(gè)部件之間的連接采用制冷劑管道連接,低溫管路外要包裹防水和保溫材料。帶冷量回收的精餾型自復(fù)疊低溫冷凝油氣分離系統(tǒng)所用的制冷劑為二元或二元以上的非共沸混合制冷劑,常見(jiàn)的組分主要有:氮?dú)?、惰性氣體、烴類、烴的鹵化物、二氧化碳等。為便于理解,上述帶冷量回收的精餾型自復(fù)疊低溫冷凝油氣分離系統(tǒng)可以分為制冷劑回路和油氣回路,以下是詳細(xì)的工作流程:在制冷劑回路中,非共沸混合制冷劑經(jīng)過(guò)壓縮機(jī)1加壓后,經(jīng)過(guò)冷凝器2被冷凝成氣液兩相的高壓流體,再進(jìn)入精餾裝置3的釜中。氣態(tài)混合制冷劑從下到上通過(guò)精餾裝置3的精餾柱,與精餾裝置3頂部流下來(lái)的回流液進(jìn)行傳熱傳質(zhì)過(guò)程;混合制冷劑中的高沸點(diǎn)組分、壓縮機(jī)潤(rùn)滑油以及少量的低沸點(diǎn)組分被冷凝下來(lái)作為回流液的一部分;大部分低沸點(diǎn)組分構(gòu)成的氣態(tài)混合制冷劑通過(guò)精餾裝置3的柱頂換熱器,從頂部出口3c流出。這股氣態(tài)混合制冷劑依次經(jīng)過(guò)第一換熱器4、第二換熱器5、第三換熱器6降溫,繼續(xù)經(jīng)過(guò)第一節(jié)流元件16節(jié)流降溫,然后進(jìn)入蒸發(fā)器7中提供冷量,再依次返流經(jīng)過(guò)第三換熱器6、第二換熱器5、第一換熱器4、精餾裝置3的柱頂換熱器,分別為油氣和精餾過(guò)程提供冷量,最終返回壓縮機(jī)1的吸氣口。以高沸點(diǎn)組分為主的液態(tài)制冷劑從精餾裝置3的底部出口3b流出,分別進(jìn)入第四換熱器12、第五換熱器13、第六換熱器14、第七換熱器15被冷凝油逐級(jí)冷卻,然后通過(guò)不同支路分別進(jìn)入第二節(jié)流元件17、第三節(jié)流元件18、第四節(jié)流元件19,經(jīng)過(guò)節(jié)流后和以低沸點(diǎn)為主的返流制冷劑在不同的位置混合。調(diào)節(jié)第二節(jié)流元件17或第三節(jié)流元件18或第四節(jié)流元件19的開(kāi)度,可以使得這股液態(tài)制冷劑和返流制冷劑以不同的比例混合,以匹配換熱器中的水當(dāng)量。以中間沸點(diǎn)組分為主的回流液從精餾裝置3的柱頂換熱器的底部出口3f流出,分別進(jìn)入第四換熱器12、第五換熱器13、第六換熱器14、第七換熱器15被冷凝油逐級(jí)冷卻,然后通過(guò)不同支路分別進(jìn)入第五節(jié)流元件20、第六節(jié)流元件21、第七節(jié)流元件22,經(jīng)過(guò)節(jié)流后和以低沸點(diǎn)為主的返流制冷劑在不同的位置混合。調(diào)節(jié)第五節(jié)流元件20或第六節(jié)流元件21或第七節(jié)流元件22的開(kāi)度,可以使得這股液態(tài)制冷劑和返流制冷劑以不同的比例混合,以匹配換熱器中的水當(dāng)量。在油氣回路中,高溫或常溫的油氣首先經(jīng)過(guò)第一換熱器4降溫,進(jìn)入第一分離器8,將部分液化下來(lái)的油品分離出來(lái);未液化的油氣繼續(xù)進(jìn)入第二換熱器5被冷卻到更低的溫度,進(jìn)入第二分離器9,將再次部分液化的油品分離出來(lái);未液化的油氣再繼續(xù)進(jìn)入第三換熱器6繼續(xù)降溫,進(jìn)入第三分離器10,將再次部分液化的油品分離出來(lái);最后,未液化的油氣進(jìn)入蒸發(fā)器7降溫,進(jìn)入第四分離器,將液化的油品分離出來(lái)。經(jīng)過(guò)系統(tǒng)各參數(shù)的調(diào)節(jié),可以保證此時(shí)未液化的油氣已經(jīng)達(dá)到了國(guó)標(biāo)中的排放標(biāo)準(zhǔn)。未利用這部分未液化油氣的冷量,將其依次返流通過(guò)第三換熱器6、第二換熱器5、第一換熱器4,復(fù)溫后以尾氣的形式排放。第一分離器8分離出來(lái)的油品從液相出口流出,進(jìn)入第四換熱器12提供冷量,復(fù)溫后排出;第二分離器9分離出來(lái)的油品從液相出口流出,依次進(jìn)入第五換熱器13和第四換熱器12提供冷量,復(fù)溫后排出;第三分離器10分離出來(lái)的油品從液相出口流出,依次進(jìn)入第六換熱器14、第五換熱器13和第三換熱器12提供冷量,復(fù)溫后排出;第四分離器11分離出來(lái)的油品從液相出口流出,依次進(jìn)入第七換熱器15、第六換熱器14、第五換熱器13和第四換熱器12提供冷量,復(fù)溫后排出。最終從第四換熱器12的第一冷凝油管道、第二冷凝油管道、第三冷凝油管道和第四冷凝油管道的出口流出的冷凝油可以匯聚起來(lái)或者分別返回儲(chǔ)罐、或者以其他方式儲(chǔ)存、或者以其他方式利用。對(duì)某石化廠裝車油氣采用本發(fā)明方法進(jìn)行低溫冷凝分離。油氣溫度為35℃,流量為30m3/h,油氣成分與濃度如表1所示:表1.油氣組成與各組分濃度組分摩爾分?jǐn)?shù)(%)組分摩爾分?jǐn)?shù)(%)甲烷0.68正戊烷0.68乙烷1.24異戊烷6.00丙烷1.70正己烷4.10正丁烷11.20氮?dú)?1.90異丁烷8.70氧氣13.80采用實(shí)施例1中所述流程,采用某種多元混合制冷劑,制冷劑回路的工況為:低壓為200kpa,高壓為2000kpa,假設(shè)壓縮機(jī)絕熱效率為85%,忽略各換熱器壓降與漏熱。利用化工軟件hysys進(jìn)行流程模擬,結(jié)果顯示:釜底的制冷劑液體在節(jié)流之前可被冷凝油預(yù)冷至約-32℃,油氣可被冷凝至-130℃,正丁烷、異丁烷、正戊烷、異戊烷、正己烷均被冷凝,尾氣中只剩下甲烷、乙烷、丙烷這些烴類,具體濃度如表2所示:表2.尾氣組成與各組分濃度組分摩爾分?jǐn)?shù)(%)甲烷0.56乙烷1.41丙烷0.11氮?dú)?5.14氧氣22.77經(jīng)核算,在該算例中,尾氣中非甲烷總烴含量約為21.5g/m3,低于國(guó)標(biāo)要求,每立方的油氣處理功耗約為0.19kw·h,相較于無(wú)冷量回收系統(tǒng)的處理功耗0.27kw·h而言有明顯的降低。實(shí)施例2如圖2所示,與實(shí)施例1連接方式與結(jié)構(gòu)相同,不同之處在于在精餾裝置底部液體出口3b與第四換熱器12的釜底液管道進(jìn)口12a之間設(shè)有干燥過(guò)濾器23和釜底換熱器24。釜底換熱器24內(nèi)設(shè)有一個(gè)高壓制冷劑管道和一個(gè)低壓制冷劑管道。具體地,精餾裝置3的底部液體出口3b與干燥過(guò)濾器23的進(jìn)口23a相連,干燥過(guò)濾器23的出口23b與釜底換熱器24的高壓制冷劑管道進(jìn)口24a相連;釜底換熱器24的高壓制冷劑管道出口24b與第四換熱器12的釜底液管道進(jìn)口12a相連;精餾裝置3的柱頂換熱器冷卻管道出口3e與釜底換熱器24的低壓制冷劑管道進(jìn)口24c相連;釜底換熱器24的低壓制冷劑管道出口24d與壓縮機(jī)1的吸氣口1a相連。在釜底換熱器24中,高壓制冷劑管道進(jìn)口24a和低壓制冷劑管道出口24d在同一側(cè),高壓制冷劑管道出口24b和低壓制冷劑管道進(jìn)口24c在另一側(cè),以實(shí)現(xiàn)冷熱流體的逆向換熱。實(shí)施例3如圖3所示,與實(shí)施例1連接方式與結(jié)構(gòu)相同,不同之處在于新增了第四換熱器單元。第四換熱器單元包括第八換熱器26、第九換熱器29以及第一截止閥25、第二截止閥27、第三截止閥28、第四截止閥30、第五截止閥31、第六截止閥32、第七截止閥33和第八截止閥34,第八換熱器26和第九換熱器29并聯(lián)設(shè)置。其中第一截止閥25與第二截止閥27聯(lián)動(dòng),第三截止閥28與第四截止閥30聯(lián)動(dòng),第五截止閥31與第六截止閥32聯(lián)動(dòng),第七截止閥33與第八截止閥34聯(lián)動(dòng)。具體地,油氣首先分別與第一截止閥25的進(jìn)口25a和第三截止閥28進(jìn)口28a相連;第一換熱器4的尾氣管道出口4f分別與第五截止閥31的進(jìn)口31a和第七截止閥33的進(jìn)口33a相連,使得尾氣分為兩條支路;第八換熱器26的油氣管道進(jìn)口26a與第一截止閥25的出口25b相連,油氣管道出口26b與第二截止閥27的進(jìn)口27a相連,尾氣管道進(jìn)口26c和第五截止閥31的出口31b相連,尾氣管道出口26d與第六截止閥32的進(jìn)口32a相連;第九換熱器29的油氣管道進(jìn)口29a與第三截止閥28的出口28b相連,油氣管道出口29b與第四截止閥30的進(jìn)口30a相連,尾氣管道進(jìn)口29c與第七截止閥33的出口33b相連,尾氣管道出口29d與第八截止閥34的進(jìn)口34a相連;第二截止閥出口27b和第四截止閥出口30b相連,匯聚成一個(gè)管道后與第一換熱器4的油氣管道進(jìn)口4g相連;第六截止閥32的出口32b和第八截止閥34的出口34b相連,匯聚成一個(gè)管道后作為尾氣的出口。第八換熱器26的油氣管道進(jìn)口26a和尾氣管道出口26d位于同一側(cè),油氣管道出口26b和尾氣管道進(jìn)口26c位于另一側(cè),以實(shí)現(xiàn)逆流換熱;第九換熱器29的油氣管道進(jìn)口29a和尾氣管道出口29d位于同一側(cè),油氣管道出口29b和尾氣管道進(jìn)口29c位于另一側(cè),以實(shí)現(xiàn)逆流換熱。系統(tǒng)的工作流程于實(shí)施例1類似,不同之處在于剛開(kāi)始運(yùn)行時(shí),同時(shí)打開(kāi)第一截止閥25、第二截止閥27、第五截止閥31和第六截止閥32,同時(shí)關(guān)閉第三截止閥28、第四截止閥30、第七截止閥33和第八截止閥34,待處理油氣和尾氣在第八換熱器26中發(fā)生熱交換,利用尾氣的余冷來(lái)預(yù)冷油氣以冷凝大部分水汽,此時(shí)第九換熱器29實(shí)施排水或除霜過(guò)程;當(dāng)系統(tǒng)運(yùn)行一段時(shí)間后,同時(shí)關(guān)閉第一截止閥25、第二截止閥27、第五截止閥31、第六截止閥32,同時(shí)打開(kāi)第三截止閥28、第四截止閥30、第七截止閥33、第八截止閥34,將油氣和尾氣的換熱過(guò)程切換到第九換熱器29中進(jìn)行,此時(shí)第八換熱器26實(shí)施排水或除霜過(guò)程。實(shí)施例4如圖4所示,帶冷量回收的精餾型自復(fù)疊低溫冷凝油氣分離系統(tǒng)包括正常濃度回路、第一變濃度回路、第二變濃度回路。正常濃度回路于實(shí)施例1中油氣分離及冷凝油冷量回收回路的連接方式與結(jié)構(gòu)類似,但在精餾柱與壓縮機(jī)之間增加了第一變濃度回路和第二變濃度回路。下面對(duì)每個(gè)回路進(jìn)行說(shuō)明:(1)正常濃度回路:正常濃度回路的部件與連接與實(shí)施例1中類似,不同之處在于:精餾裝置3的柱頂換熱器頂部的出口3c分別與兩條并聯(lián)支路相連,其中一條支路與第一換熱器4的正流制冷劑管道進(jìn)口4a相連,另一條支路與第十一截止閥38的進(jìn)口38a相連;精餾裝置3的精餾柱底部出液口3b分別與四條并聯(lián)支路相連,即分別與第二節(jié)流元件17的進(jìn)口17a、第三節(jié)流元件18的進(jìn)口18a、第四節(jié)流元件19的進(jìn)口19a以及第九截止閥35的進(jìn)口35a相連。(2)第一變濃度回路:第一變濃度回路由依次串聯(lián)設(shè)置的第九截止閥35、儲(chǔ)液罐36和第十截止閥37組成。其中第九截止閥35的進(jìn)口35a與精餾裝置3的底部出口3b相連,出口與儲(chǔ)液罐36的進(jìn)口36a相連;第十截止閥37的進(jìn)口37a與儲(chǔ)液罐36的出口36b相連,出口37b與壓縮機(jī)1的吸氣口1a相連。(3)第二變濃度回路:第二變濃度回路由依次串聯(lián)設(shè)置的第十一截止閥38、第一儲(chǔ)氣罐39和第十二截止閥40組成。其中第十一截止閥38的進(jìn)口38a與精餾裝置3的頂部出口3c相連,出口38b與第一儲(chǔ)氣罐39的進(jìn)口39a相連;第十二截止閥40的進(jìn)口40a與第一儲(chǔ)氣罐39的出口39b相連,出口40b與壓縮機(jī)1的吸氣口1a相連。該實(shí)施方式中的第九截止閥35、第十截止閥37、第十一截止閥38、第十二截止閥40為手動(dòng)或者自動(dòng)雙向截止閥。為便于理解,以下是詳細(xì)的工作流程:制冷劑的正常濃度回路、油氣分離回路工作流程與實(shí)施例1中所述相同,不同之處在于開(kāi)機(jī)前要確認(rèn)第九截止閥35、第十截止閥37、第十一截止閥38、第十二截止閥40都處于關(guān)閉狀態(tài)。隨著時(shí)間延續(xù),油氣分離系統(tǒng)的制冷溫度不斷下降,在足夠長(zhǎng)的時(shí)間之后,在環(huán)境溫度以及油氣熱負(fù)荷不變的情況下,系統(tǒng)達(dá)到穩(wěn)定運(yùn)行狀態(tài),制冷溫度在混合制冷劑的正常濃度下達(dá)到了最低極限。此時(shí),分別啟動(dòng)第一變濃度回路和第二變濃度回路就可以實(shí)現(xiàn)更低的制冷溫度。啟用第一變濃度回路:打開(kāi)第九截止閥35,將富含高沸點(diǎn)組分的混合制冷劑從精餾柱底部引入儲(chǔ)液罐36中,一段時(shí)間后關(guān)閉第九截止閥35,使得正常濃度回路中高沸點(diǎn)組分制冷劑減少,提高了參與循環(huán)的制冷劑中低沸點(diǎn)組分的濃度,能比正常濃度制冷實(shí)現(xiàn)更低的制冷溫度,可以將油氣中的輕烴類處理得更徹底。啟用第二變濃度回路:打開(kāi)第十二截止閥40,將富含低沸點(diǎn)組分的混合制冷劑從第一儲(chǔ)氣罐39中放出,一段時(shí)間后關(guān)閉第十二截止閥40,使得正常濃度回路中參與循環(huán)的低沸點(diǎn)制冷劑增加,因此提高了參與循環(huán)的低沸點(diǎn)組分濃度,可以比正常濃度和啟用第一變濃度回路后的制冷實(shí)現(xiàn)更低的溫度。經(jīng)過(guò)足夠長(zhǎng)時(shí)間運(yùn)行后,在環(huán)境溫度和熱負(fù)荷不變的情況下,系統(tǒng)再次達(dá)到穩(wěn)定狀態(tài),制冷溫度在改變后的制冷劑濃度下達(dá)到了新的最低極限。關(guān)機(jī)前,依次停用第二變濃度回路和第一變濃度回路,可以逐步減小停機(jī)時(shí)混合制冷劑中的低沸點(diǎn)組分濃度。停用第二變濃度回路:打開(kāi)第十一截止閥38,將富含低沸點(diǎn)組分的混合制冷劑儲(chǔ)存到第一儲(chǔ)氣罐39中,一段時(shí)間后關(guān)閉第十一截止閥38,使得參與循環(huán)的制冷劑低沸點(diǎn)組分濃度繼續(xù)減小。停用第一變濃度回路:打開(kāi)第十截止閥37,將儲(chǔ)液罐36中富含高沸點(diǎn)組分的混合制冷劑放出,一段時(shí)間后關(guān)閉第十截止閥37,使得參與循環(huán)的制冷劑低沸點(diǎn)組分濃度繼續(xù)減小。在停用兩個(gè)變濃度回路后即可停機(jī),這兩個(gè)變濃度回路可在下一次開(kāi)機(jī)運(yùn)行中繼續(xù)啟用單個(gè)或者兩個(gè)同時(shí)啟用。實(shí)施例5如圖5所示,與實(shí)施例4的結(jié)構(gòu)及連接方式相同,不同之處在于:在第一節(jié)流元件16的進(jìn)口16a和第三換熱器6的高壓制冷劑管道出口6b之間設(shè)有第五分離器44,第五分離器44與壓縮機(jī)1的吸氣口1a之間設(shè)有第三變濃度回路;第三變濃度回路由依次串聯(lián)的第十三截止閥41、第二儲(chǔ)氣罐42、第十四截止閥43組成;其中,第十三截止閥41的進(jìn)口41a與第五分離器44的氣相出口44c相連,出口41b與第二儲(chǔ)氣罐42的進(jìn)口42a相連;第十四截止閥43的進(jìn)口43a與第二儲(chǔ)氣罐42的出口42b相連,出口43b與壓縮機(jī)1的吸氣口1a相連。啟用第一和第二變濃度回路的方法和實(shí)施例4相同。啟用第三變濃度回路:打開(kāi)第十四截止閥43,將低沸點(diǎn)組分比例更高的混合制冷劑從第二儲(chǔ)氣罐42中放出,一段時(shí)間后關(guān)閉第十四截止閥43,使得參與循環(huán)的制冷劑低沸點(diǎn)組分濃度提高,可以比正常濃度制冷、啟用第一變濃度回路制冷、啟用第二變濃度回路制冷實(shí)現(xiàn)更低的制冷溫度。經(jīng)過(guò)足夠長(zhǎng)時(shí)間運(yùn)行后,在環(huán)境溫度和熱負(fù)荷不變的情況下,系統(tǒng)再次達(dá)到穩(wěn)定狀態(tài),制冷溫度在改變后的制冷劑濃度下達(dá)到了新的最低極限。關(guān)機(jī)前,依次停用第三變濃度回路、第二變濃度回路和第一變濃度回路,可以逐步減小停機(jī)時(shí)混合制冷劑中的低沸點(diǎn)組分濃度。停用第三變濃度回路:打開(kāi)第十三截止閥41,將低沸點(diǎn)組分含量最多的混合制冷劑儲(chǔ)存到第二儲(chǔ)氣罐42中,一段時(shí)間后關(guān)閉第十三截止閥41,使得參與循環(huán)的制冷劑低沸點(diǎn)濃度繼續(xù)減小。停用第二變濃度回路和停用第一變濃度回路方法和實(shí)施例4相同。以上所述僅為本發(fā)明的較佳實(shí)施舉例,并不用于限制本發(fā)明,凡在本發(fā)明精神和原則之內(nèi),所作的任何修改、等同替換、改進(jìn)等,均應(yīng)包含在本發(fā)明的保護(hù)范圍之內(nèi)。當(dāng)前第1頁(yè)12