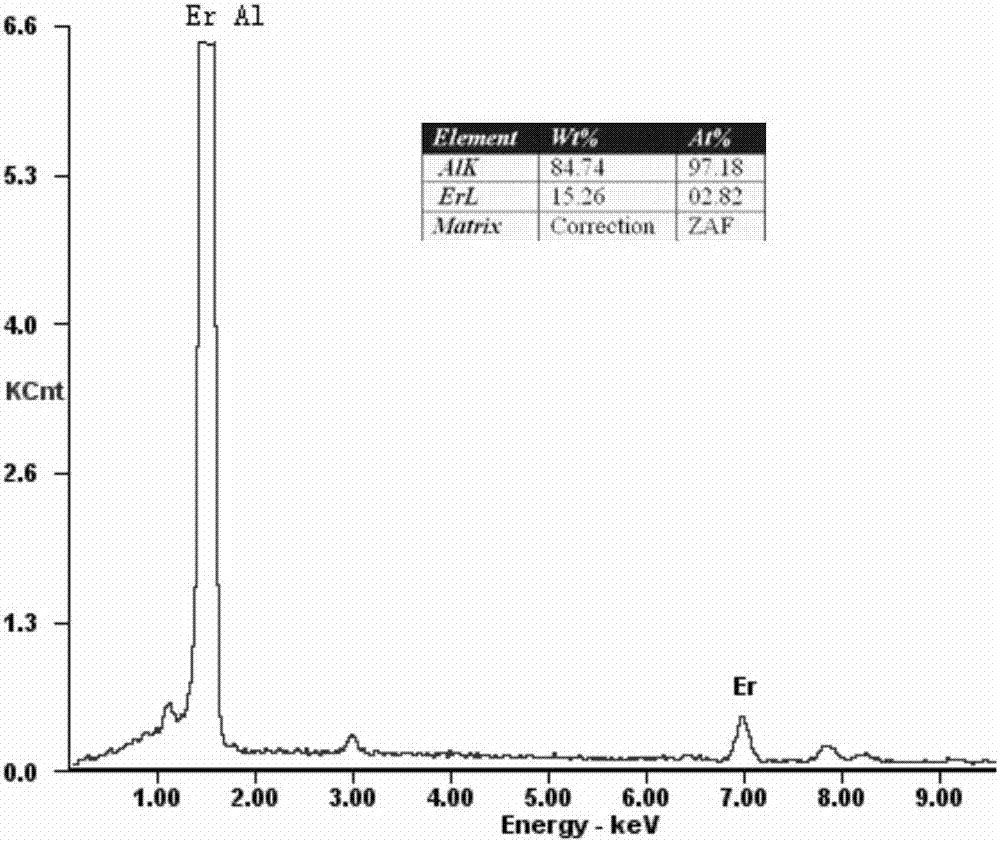
本發(fā)明涉及一種輕質高導耐熱鋁導線及其制備方法,屬于電工材料技術領域。技術背景根據(jù)能源互聯(lián)的戰(zhàn)略部署,我國電網(wǎng)將實現(xiàn)“西電東送,南北互供、全國聯(lián)網(wǎng)”,輸電線路距離遠、輸電容量大、自然環(huán)境復雜,為了降低輸送線損、減少線路建設成本、節(jié)約緊張的走廊資源,對輸電導線提出了更高的要求,既要有高電導率,又要有良好的耐熱性能和抗弧垂特性。因此,研發(fā)一種具有高導電率、良好的耐熱性能、密度小的鋁導線,成為業(yè)內(nèi)亟需解決的技術難題。金屬中的自由電子在外加電場作用下發(fā)生定向運動形成電流,而晶格場周期性的異常點(或不規(guī)則點)會阻礙電子的定向運動并對電子波產(chǎn)生散射作用。金屬材料的導電性跟自由電子的平均自由程(相鄰異常點間距的平均值)緊密相關,自由電子的平均自由程越小,材料電導率越低。金屬中的雜質元素、固溶原子以及晶體缺陷都會導致晶格場局部偏離其周期性位置,縮短自由電子的平均自由程,從而導致金屬電導率的降低。雜質對電導率的影響與雜質元素的種類、含量、在金屬中存在的狀態(tài)緊密相關,工業(yè)純鋁中不可避免的雜質元素Ti、V、Cr、Mn等對導電性影響較大,特別是較高含量的雜質元素固溶于鋁基體時,會大幅降低鋁導體的電導率。固溶原子導致晶格畸變而破壞金屬庫侖勢場的周期性,并成為對導電電子的散射中心,固溶原子摩爾濃度越大,相鄰散射中心間的距離越小,電子的平均自由程越小,電導率越低,以Zr為例,少量Zr原子固溶于鋁基體中便會顯著降低合金的電導率。純度為99.99%的高純Al在20℃的電導率高達64.94%IACS,密度為2.7g/cm3,但強度僅為80~100MPa,再結晶溫度為150℃左右。添加0.6~0.9wt.%Mg、0.5~0.9wt.%Si、0.5wt.%Fe、0.1wt.%Cu、0.1wt.%Zn的6021合金是常用的高強度電工鋁合金,抗拉強度可達到295~325MPa,但是,其20℃時的導電率僅為52.5~55%IACS。旨在提高鋁導體耐熱性和強度的微合金化,特別是當合金組分及配比設計不當時,會對導電性能產(chǎn)生非常不利的影響,研發(fā)輕質高導耐熱鋁導線的技術難點是在導電性、耐熱性、比強度之間尋求最佳平衡點。通常,導電率和耐熱性呈此消彼長的關系,現(xiàn)有公開的技術方案中往往存在著顧此失彼的情況,導電率高的技術方案,耐熱性不理想,耐熱性好的技術方案,導電率不夠理想。公開號為CN102230113A的專利,公開的成分為0.06~0.15wt.%Zr,0.15~0.30wt.%Er,0.1~0.2wt.%Fe,通過Zr、Er、Fe的微合金化,采用連鑄連軋工藝,制備出的鋁電線,導電率只有59.5~60.5%IACS,短時耐熱溫度為210℃,長期耐熱溫度為180℃,抗拉強度為157MPa,沒有公開合金的密度參數(shù)。公開號為CN103498083A的專利,公開的成分為0.01~0.2wt.%Er,0~0.3%wt.Zr,0~0.2wt.%B,從其實施例記載的參數(shù)來看,含有Er、Zr、B的實施例的導電率僅為60%IACS,而只含Er、Zr元素中的一種或兩種的實施例的導電率只有58%IACS,且沒有公開合金密度、強度、耐熱性能參數(shù)及連鑄連軋的工藝參數(shù)。因此,通過優(yōu)化合金組分及制備工藝,在不降低電導率的前提下,提高鋁導線的耐熱性和比強度,制備輕質、高導、耐熱鋁導線是本領域長期以來的追求。
技術實現(xiàn)要素:本發(fā)明的目的在于克服現(xiàn)有技術之不足而提供一種組分配比合理、合金化元素少、工藝簡單且靈活、生產(chǎn)成本低的輕質高導耐熱鋁導線及制備方法。本發(fā)明通過微量添加對導電率損害較小的合金元素,產(chǎn)生凈化、變質、細化和彌散強化作用,相對99.99%的高純鋁,在電導率下降很少的前提下,大幅提高導線的耐熱性和比強度,從而滿足大容量遠距離輸電線路的輕質、高導、耐熱的服役要求。本發(fā)明一種輕質高導耐熱鋁導線,包括下述組分按質量百分比組成:B:0.035~0.06wt.%;Zr:0.1~0.2wt.%;Er:0.2~0.4wt.%(但不包含0.2wt%);Ti、V、Cr、Mn雜質元素總含量小于等于0.01wt.%,其余為Al;其中,Zr、Er按質量比Zr:Er=1:1.5~2.5添加,優(yōu)選Zr、Er按質量比Zr:Er=1:1.5~2添加。本發(fā)明一種輕質高導耐熱鋁導線的制備方法,包括下述步驟:第一步:將工業(yè)純鋁錠加熱至740℃~780℃熔化,按設計的鋁導線組分中Zr、Er的質量百分比配取Al-Zr和Al-Er中間合金加入鋁熔體中,待中間合金完全熔化并攪拌均勻后,對Zr、Er、Al合金熔體進行爐前快速成分分析,并將合金熔體降至720℃~730℃保溫,同時添加Al-B中間合金進行精煉,然后靜置、扒渣、鑄造,得到坯料;第二步:將坯料退火后,進行擠壓、拉撥成單絲。本發(fā)明一種輕質高導耐熱鋁導線的制備方法,所述Al-B中間合金的添加量由以下兩部分確定:第一,按設計組分中B的質量百分比配取的Al-B中間合金;第二,按B的質量為Zr、Er、Al合金熔體中Ti、V、Cr、Mn雜質元素總含量的2-5倍配取的Al-B中間合金。本發(fā)明一種輕質高導耐熱鋁導線的制備方法,所述鑄造方式可根據(jù)生產(chǎn)線設備配置情況變換,既可通過普通鑄造或半連續(xù)鑄造獲得錠坯,也可通過連續(xù)鑄造獲得桿坯。本發(fā)明一種輕質高導耐熱鋁導線的制備方法,鑄造時,鑄錠以20-300℃/s的速度冷卻至室溫。本發(fā)明一種輕質高導耐熱鋁導線的制備方法,鑄造時采用水冷鑄造。本發(fā)明一種輕質高導耐熱鋁導線的制備方法,所述坯料的退火工藝為:退火溫度為480℃~500℃,保溫1-10h后隨爐冷卻。本發(fā)明一種輕質高導耐熱鋁導線的制備方法,所述擠壓方式可根據(jù)生產(chǎn)線設備配置情況進行變換,既可采用加熱的錠坯進行常規(guī)熱擠壓,也可采用室溫桿坯進行連續(xù)擠壓,所述熱擠壓溫度為300~450℃。本發(fā)明一種輕質高導耐熱鋁導線的制備方法,熱擠壓或室溫連續(xù)擠壓的擠壓比大于等于80,擠壓總變形量大于等于80%。本發(fā)明一種輕質高導耐熱鋁導線的制備方法,所述拉拔采用擠壓桿料進行多道次冷拉拔,可根據(jù)實際需要確定拉拔坯料直徑,特別是可根據(jù)服役強度要求確定所用坯料直徑,并通過不同的拉撥變形量來調控單絲的強度。本發(fā)明一種輕質高導耐熱鋁導線的制備方法,擠壓后進行多道次拉撥,道次延伸系數(shù)為1.2~1.5,累計總延伸系數(shù)為5.5~10.5,可采用普通潤滑油或乳濁液進行潤滑,乳濁液還可起冷卻作用,以使鋁絲的溫度不超過180℃。本發(fā)明一種輕質高導耐熱鋁導線的制備方法,所制備的導線,密度小于等于2.71g/cm3,在20℃的電導率大于等于62%IACS,短時耐熱溫度高達230℃,長期耐熱溫度高達210℃,抗拉強度大于等于165MPa。本發(fā)明原理和優(yōu)勢根據(jù)金屬導電理論,雜質和晶體缺陷對鋁的導電性影響很大,雜質含量越少、晶格畸變和晶界等晶體缺陷越少,金屬晶體的導電性越好,在工業(yè)純鋁的不可避免的雜質中,Ti、V、Cr、Mn對導電性的有害影響較大,特別是當其以固溶形式存在于鋁基體時。本發(fā)明B的添加量為按設計的鋁導線組分中B的質量百分比(0.035-0.06wt.%)和工業(yè)純鋁中Ti、V、Cr、Mn雜質元素總含量的2-5倍確定的B的質量之和,在滿足B元素作為精煉劑和變質劑的前提下,B、Zr、Er的協(xié)同作用帶來了預料不到的技術效果。本發(fā)明的合金熔煉過程中,Al-B中間合金的添加量按兩部分確定,合金熔體中B含量遠遠超過0.06wt.%,其作為精煉劑和變質劑。首先,B作為精煉劑時,與工業(yè)純鋁中不可避免的Ti、V等雜質反應,生成比重較大的硼化物,以爐渣的形式被除去(見附圖2、附圖3),從而大幅提高鋁導體的電導率。其次,富余的B作為變質劑,產(chǎn)生變質作用,可以使沿晶界連續(xù)分布的富Fe相變?yōu)椴贿B續(xù)的顆粒狀,既可以改善鋁導線的導電性能的同時,也可提高其強度和熱穩(wěn)定性,同時,可以降低對原材料工業(yè)純鋁錠的純度要求,從而大幅度降低合金制備成本。發(fā)明人發(fā)現(xiàn):如果加入的精煉劑和變質劑的B含量太少,使合金基體中B含量小于0.035%,則會降低材料的電導率,但是,如果加入過量的B作為精煉劑和變質劑(B含量為Ti、V總含量的8倍),則鋁中會出現(xiàn)較多粗大的Al、B的化合物,也會明顯降低材料的電導率。Er元素傾向于吸附在α-Al晶核上,生成Al3Er阻礙α-Al枝晶成長,達到細化二次枝晶組織的效果,初生的Al3Er被推擠到晶界,在熔體最后完全凝固時形成含α-Al相和Al3Er相的共晶化合物。作為稀土元素,Er也可與Fe等雜質元素形成化合物,產(chǎn)生凈化和變質作用。附圖6為對比例2中的第二相粒子及能譜分析結果,對比例2未添加B,圖6(b)顯示晶內(nèi)可能形成了Al3Er和(Al,Fe)的混合相,或(Al,Fe,Er)三元化合物,沒有B的作用,Er元素更傾向于與雜質元素形成化合物或者形成Al3X相。本發(fā)明的優(yōu)勢是利用B和Zr、Er的協(xié)同作用,由B來產(chǎn)生除雜和變質作用,抑制含Er雜質相的形成,并通過鑄造過程的快速冷卻抑制粗大的初生相形成,使Zr和Er主要以亞穩(wěn)定的過飽和固溶態(tài)存在,從而促使后續(xù)退火過程析出大量與基體共格的Al3(Er,Zr)復合粒子,如附圖5所示。本發(fā)明Al3(Er,Zr)三元相析出的原理是:退火過程中,擴散速率較快的Er在基體中率先形成粒子,為Zr的脫溶析出提供形核質點,促進Al-Zr固溶體的分解,擴散速率較慢的Zr聚集在Al3Er粒子的外層,形成與基體共格的、L12結構的、納米級的球狀Al3(Er,Zr)復合粒子。本發(fā)明析出納米尺度的Al3(Er,Zr)復合粒子有如下優(yōu)勢:一方面,降低Zr和Er在鋁基體中的固溶程度,提高鋁導線的電導率,另一方面,彌散分布的與晶體共格的納米尺度的Al3(Er,Zr)復合粒子,對位錯、亞晶、晶界產(chǎn)生釘扎作用,具有明顯的強化作用及抑制再結晶作用,能有效提高鋁導體的強度和耐熱性。本發(fā)明采用鑄造、退火、擠壓、拉撥的制備工藝,能夠區(qū)別其他鋁導線的連鑄連軋工藝,具有生產(chǎn)流程短、工藝控制簡單靈活的優(yōu)勢,制備的導線在保證較高導電率的前提下,具有較好的耐熱性和比強度。本發(fā)明的快速冷卻鑄造有一定抑制粗大初生相形成的作用,使鑄坯具有較高過飽和固溶度,為后續(xù)退火工序析出細小彌散分布的第二相粒子提供驅動力。本發(fā)明的鑄坯高溫短時退火,其主要作用是析出大量彌散分布的第二相粒子,尤其是析出很多與晶體共格的納米尺度的Al3(Er,Zr)復合粒子,其次要作用是適當消除坯料的成分偏析、組織偏析及鑄造應力,從而改善鑄造組織和加工性能,此外,相對鋁合金的均勻化退火時間及已公開專利的退火時間,本發(fā)明的退火時間較短,具有節(jié)能降耗優(yōu)勢。本發(fā)明采用擠壓進行塑性變形,具有生產(chǎn)靈活、工藝控制簡單的優(yōu)勢,既可采用錠坯一次擠壓成線桿,也可采用連續(xù)鑄造的桿坯連續(xù)擠壓成較小直徑的線坯,相比軋制變形,具有更大的變形程度和更強烈的三向壓應力狀態(tài),可大大改善鑄造組織和提高后續(xù)加工性能。本發(fā)明采用擠壓桿料進行多道次冷拉拔獲得鋁合金單絲,可根據(jù)實際需要確定桿料直徑,特別是可根據(jù)服役強度要求確定所用桿料直徑,并通過不同拉撥變形量來調控單絲的強度。綜上所述,本發(fā)明基于Al、B、Zr、Er元素的合理配比和含B精煉劑的適量加入,通過快速冷卻鑄造、鑄坯的高溫短時退火、大變形量的擠壓,使B產(chǎn)生凈化、變質及協(xié)同Zr、Er的復合微合金化作用,制備出的導線在20℃的電導率大于等于62%IACS,長期耐熱溫度高達210℃,短時耐熱溫度高達230℃,抗拉強度大于等于165MPa,密度(≤2.71g/cm3)與純鋁的密度2.7g/cm3比較接近,可提高輸電線路容量和降低輸送線損,具有良好的抗弧垂特性和耐熱性能,可增加輸電線路塔桿的間距和提高遠距離、大容量輸電線路的安全穩(wěn)定性和服役壽命。本發(fā)明生產(chǎn)流程短、工藝控制簡單靈活且要求較低,加入的合金化元素數(shù)目少、含量低,節(jié)省了昂貴稀土元素的用量,對原材料雜質含量和鑄坯質量沒有嚴格要求,能源消耗也不高,因此,還具有生產(chǎn)成本較低的優(yōu)勢。附圖說明附圖1(a)為實施例1的鑄態(tài)金相組織,附圖1(b)為實施例2的鑄態(tài)金相組織,附圖1(c)為實施例3的鑄態(tài)金相組織;附圖2為本發(fā)明實施例2熔煉爐渣的微觀組織照片,附圖3為附圖2中質點的能譜分析結果;附圖4(a)為對比例2合金的金相組織照片,附圖4(b)為實施例2合金的金相組織照片,附圖4(c)為對比例1合金的金相組織照片;附圖5(a)為實施例2合金的低倍率TEM照片,附圖5(b)為實施例2合金的高倍率TEM照片,附圖5(c)為實施例2合金中Al3(Er,Zr)復合粒子的高分辨TEM形貌;附圖6(a)為對比例2合金退火態(tài)合金的微觀組織形貌,附圖6(b)為附圖6(a)中標識處A點析出相能譜分析結果,附圖6(c)為附圖6(a)中標識處B點析出相能譜分析結果,附圖6(d)為附圖6(a)中標識處C點析出相能譜分析結果;附圖7~附圖10為實施例2所制備的Φ4鋁導線的性能檢測報告。由圖1(a)、圖1(b)、圖1(c)可以看出,Zr、Er元素的聯(lián)合添加具有明顯的晶粒細化效果,并且Zr、Er元素的含量越大,晶粒細化效果越明顯。由圖2、圖3所示實施例2爐渣的微觀組織形貌及能譜分析結果可以看出:存在不同于白色AlFe相的另一種相,該相呈現(xiàn)出四周較暗中間亮白的特點,能譜分析結果顯示,該相為含Al、B、Ti、V的相,說明雜質Ti、V確實與B形成了化合物而進入爐渣,這是使得合金電導率提高的重要原因之一。由圖4(a)可以看出,不用B作精煉劑時,晶界分布著較多連續(xù)的雜質相;由圖4(b)可以看出,采用合適質量比例的硼精煉劑后,基體中出現(xiàn)了較多的點狀相,晶界的連續(xù)相也轉變?yōu)椴贿B續(xù)的條狀及點狀;由圖4(c)可以看出,采用過量的B作為精煉劑后,基體中出現(xiàn)了較多粗大的第二相,能譜分析結果表明為Al、B的化合物。結合對比例2中的材料導電率較低的事實,說明添加過量的B對材料的電導率有負面影響。在圖5(a)所示析出相周圍可以觀察到清晰的Ashby-Brown應力襯度,析出相仍與基體保持良好的共格性,圖5(b)所示析出相的外殼和內(nèi)核表現(xiàn)出了明顯的襯度差異,圖5(c)所示區(qū)域可分為基體、析出相的殼、析出相的核3個部分,析出相的殼的選區(qū)電子衍射斑點對應L12結構,析出相外殼對應的衍射強度比內(nèi)核要強,確定為一種內(nèi)部富含Er、外部殼富含Zr的Al3(Er1-xZrx)復合相。圖5(a)、圖5(b)、圖5(c)證明本發(fā)明合金退火過程中析出了大量與基體共格的納米尺度的Al3(Er,Zr)復合相粒子,從而保障了電導率和耐熱性及強度的協(xié)調發(fā)展。圖6(a)-(d)為對比例2中的第二相粒子及能譜分析結果,圖6(b)顯示晶內(nèi)A點可能是Al3Er和(Al,Fe)的混合相,也可能是(Al,Fe,Er)三元化合物,圖6(c)顯示晶界B點顆粒相為Al3Er相,圖6(d)顯示晶界C點針狀相為Al3Fe相。對比例2未添加B,Er元素更傾向于與雜質元素形成化合物或者形成Al3X相,證明B元素有促進Al3(Er1-xZrx)三元復合相析出的作用。附圖7~附圖10可知,本發(fā)明實施例2所制備的鋁導線在20℃的電導率達到了62%IACS,短期耐熱溫度達到230℃(230℃保溫1h抗拉強度殘留率高達92%,抗拉強度為165MPa,可作為本發(fā)明導線性能優(yōu)越性的有力支撐材料。具體實施方式實施例1以純度大于99.7%的工業(yè)純鋁錠、Al-11.34%Zr中間合金和Al-4.7%Er中間合金為原料,先將工業(yè)純鋁在760℃熔化后,加入Al-Zr、Al-Er中間合金,待中間合金完全熔化并攪拌均勻后,對Zr、Er、Al合金熔體進行爐前快速成分分析,并將合金熔體降至730℃保溫,再按合金熔體中雜質元素Ti、V總含量的2倍及合金中B的質量百分比,加入Al-2.5%B中間合金進行精煉,使各元素的質量百分比為:B為0.035wt.%,Zr為0.1wt.%,Er為0.21wt.%,Ti、V、Cr、Mn等雜質元素總和為0.001wt.%,Al為余量。然后依次進行攪拌、靜置、扒渣,水冷鑄造。壞料在480℃保溫10h隨爐冷卻,隨后在420℃進行熱擠壓,擠壓比為89.7,擠壓變形量為98.7%,得到Φ9.5的圓鋁桿,經(jīng)5道次拉拔成Φ4.0mm的鋁導線。對鋁導線進行導電率、抗拉強度、耐熱性能、密度測試,結果如表1所示。實施例2以純度大于99.7%的工業(yè)純鋁錠、Al-11.34%Zr和Al-4.7%Er中間合金為原料,將工業(yè)純鋁在760℃熔化后,加入Al-Zr、Al-Er中間合金,待中間合金完全熔化并攪拌后,對Zr、Er、Al合金熔體進行爐前快速成分分析,并將合金熔體降至730℃保溫,再按合金熔體中雜質元素Ti、V總含量的3.5倍及合金中B的質量百分比,加入Al-2.5%B中間合金進行精煉,使各元素的質量百分比為:B為0.05wt.%,Zr為0.1wt.%,Er為0.21wt.%,Ti、V、Cr、Mn等雜質元素總和為0.001wt.%,Al為余量。然后依次進行攪拌、靜置、扒渣,水冷鑄造。壞料在490℃保溫8h隨爐冷卻,隨后在420℃進行熱擠壓,擠壓比為89.7,擠壓變形量為98.7%,得到Φ9.5的圓鋁桿,經(jīng)5道次拉拔成Φ4.0mm的鋁導線。對鋁導線進行導電率、抗拉強度、耐熱性能、密度測試,結果如表2所示。實施例3以純度大于99.7%的工業(yè)純鋁錠、Al-11.34%Zr中間合金和Al-4.7%Er中間合金為原料,將工業(yè)純鋁在760℃熔化后,加入Al-Zr、Al-Er中間合金,待中間合金完全熔化并攪拌后,對Zr、Er、Al合金熔體進行爐前快速成分分析,并將合金熔體降至730℃保溫,再按合金熔體中雜質元素Ti、V總含量的5倍及合金中B的質量百分比,加入Al-2.5%B中間合金精煉后,各元素的質量百分比為:B為0.06wt.%,Zr為0.2wt.%,Er為0.4wt.%,Ti、V、Cr、Mn等雜質元素總和為0.001wt.%,Al為余量。然后依次進行攪拌、靜置、扒渣,水冷鑄造。坯料在500℃保溫1h隨爐冷卻,隨后在420℃進行熱擠壓,擠壓比為89.7,擠壓變形量為98.7%,得到Φ9.5的圓鋁桿,經(jīng)5道次拉拔成Φ4.0mm的鋁導線。對鋁導線進行導電率、抗拉強度、耐熱性能、密度測試,結果如表3所示。對比例1以純度大于99.7%的工業(yè)純鋁錠、Al-11.34%Zr中間合金和Al-4.7%Er中間合金為原料,將工業(yè)純鋁在760℃熔化后,加入Al-Zr、Al-Er中間合金,待中間合金完全熔化并攪拌后,對Zr、Er、Al合金熔體進行爐前快速成分分析,并將合金熔體降至730℃保溫,再按合金熔體中雜質元素Ti、V總含量的8倍及合金中B的質量百分比,加入Al-2.5%B中間合金精煉后,各元素的質量百分比為:B為0.10wt.%,Zr為0.1wt.%,Er為0.21wt.%,Ti、V、Cr、Mn等雜質元素總和為0.001wt.%,Al為余量。然后依次進行攪拌、靜置、扒渣,水冷鑄造。坯料在490℃保溫8h后隨爐冷卻,隨后在420℃進行熱擠壓,擠壓比為89.7,擠壓變形量為98.7%,得到Φ9.5的圓鋁桿,經(jīng)多道次拉拔成Φ4.0mm的鋁導線。對鋁導線進行導電率、抗拉強度、耐熱性能、密度測試,結果如表5所示。對比例2按照工業(yè)純鋁、Zr0.2%,Er0.4%進行配料,其原料為純度大于99.7%的工業(yè)純鋁錠、Al-11.34%Zr中間合金、Al-4.7%Er中間合金。將工業(yè)純鋁在760℃熔化后,加入Al-Zr、Al-Er中間合金,待中間合金完全熔化并攪拌后,對Zr、Er、Al合金熔體進行爐前快速成分分析,并將合金熔體降至730℃保溫,依次進行攪拌、靜置、扒渣,水冷鑄造。鑄錠在500℃保溫1h隨爐冷卻,隨后在420℃進行熱擠壓,擠壓比為89.7,擠壓變形量為98.7%,得到Φ9.5的圓鋁桿,經(jīng)5道次拉拔成Φ4.0mm的鋁導線。對鋁導線進行導電率、抗拉強度、耐熱性能、密度測試,結果如表4所示。本發(fā)明3個實施例得到的鋁合金導線,密度均小于等于2.71g/cm3,在20℃常溫下導電率大于等于62%IACS,短時耐熱溫度達到230℃,長期耐熱溫度達到210℃。對比例1加入了過量的B,其他組分和實施例1和實施例2相同,退火工藝與實施例2相同,對比例2除了未加入B元素外,其他組分與實施例3相同,2個對比例的電導率均低于61%IACS,在230℃退火1小時的強度殘存率均低于90%,在230℃退火400小時的強度殘存率也低于90%。從以上實施例與對比例所得到的性能參數(shù)可知:作為精煉劑和變質劑的B,如果加入含量太少,導致合金基體中B含量小于0.035wt.%,或者加入量過多,如加入Ti、V總含量8倍的B,均會降低導線的導電性能和耐熱性能。