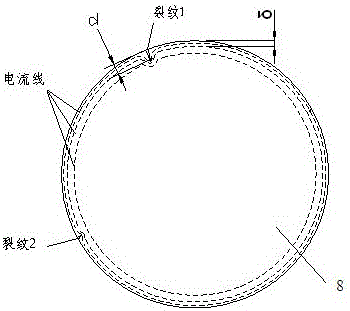
本發(fā)明涉及一種軋輥表面微裂紋的處理方法,尤其涉及一種通過高頻感應(yīng)處理使軋輥表面微裂紋得到鈍化、愈合,以延長軋輥使用壽命的處理方法。
背景技術(shù):軋輥在使用過程表面常常存在大量微裂紋,其產(chǎn)生來源主要有:(1)軋輥工作時,輥面由于在巨大的軋制力作用下與軋件周期性接觸而產(chǎn)生大量疲勞微裂紋,深度約0.1~0.3mm。(2)軋輥下機磨輥時,目的是消除輥面缺陷層,但如果磨削刀具選擇不當(dāng)、潤滑冷卻不良、進(jìn)刀量過大等,也可能對輥面造成損傷,產(chǎn)生磨削微裂紋。因此,輥面微裂紋的存在不僅增大了輥子磨削量,縮短了軋輥使用時間,而且以磨削后殘留微裂紋為裂紋起源,在軋輥工作過程裂紋進(jìn)一步擴展,可能釀成軋輥剝落甚至斷裂等重大軋輥事故。為此,軋鋼企業(yè)結(jié)合渦流探傷檢測,在軋輥每個軋制周期結(jié)束下機后,一般需要磨削掉0.2mm厚度的輥面,以消除缺陷。在軋輥使用后期,考慮到輥面裂紋殘留積累,往往在幾次周期的少磨削之后采取一次加大磨削量甚至到1~2mm的方法來徹底清除軋輥輥面缺陷層,防止軋輥異常失效,這無疑更加速了軋輥消耗。因此,尋求合理的輥面微裂紋處理技術(shù)對軋輥的使用來說就顯得十分重要。關(guān)于表面裂紋的修復(fù)方法,中國專利200610027025.6對大裂紋直接用螺栓進(jìn)行機械“縫補”;中國專利98100663.9對滲碳工件在磨削前采用熱處理消除表面淬火馬氏體來防止后續(xù)磨削產(chǎn)生裂紋;中國專利200710190071.2采用激光沖擊實現(xiàn)止裂;中國專利200510046729.3、中國專利00120516.1為焊補法;中國專利200610150952.7、中國專利200710185705.5均采用脈沖電磁場對焊縫裂紋進(jìn)行處理,防止或減少焊接裂紋。此外,對尺寸較大的裂紋也有采用打“止裂孔”來防止裂紋繼續(xù)擴展的方法。但是,這些方法對消除軋輥表面微裂紋來說要么無能為力(如螺栓縫補法、焊補法、打止裂孔等),要么可能會對輥面造成物理損傷(激光沖擊法、電磁脈沖法等)。
技術(shù)實現(xiàn)要素:本發(fā)明的目的在于提供一種軋輥表面微裂紋的處理方法,該方法通過感應(yīng)電流在裂紋尖端的熱效應(yīng)來鈍化或焊合軋輥表面微裂紋,降低軋輥磨削量,防止軋輥異常失效,從而延長軋輥使用壽命。為實現(xiàn)上述發(fā)明目的,本發(fā)明采用了如下技術(shù)方案:一種軋輥表面微裂紋的處理方法,在有微裂紋的軋輥表面通過電磁感應(yīng)裝置在軋輥表面產(chǎn)生感應(yīng)電流,利用感應(yīng)電流使裂紋尖端位置局部得到加熱升溫,鈍化裂紋尖端,并且在裂紋尖端能焊合微裂紋,使軋輥表面微裂紋得到愈合。調(diào)節(jié)所述電磁感應(yīng)裝置的電源輸出頻率,使感應(yīng)電流在軋輥表面的集膚深度δ與微裂紋的深度d基本相當(dāng),集膚深度δ按照δ=1/sqrt(π*μ*σ*f)計算,其中μ是軋輥磁導(dǎo)率,σ是軋輥電導(dǎo)率,f是所施加的交流電頻率。優(yōu)選的,對于0.1~0.3mm深的軋輥表面疲勞微裂紋,所述電磁感應(yīng)裝置的電源輸出頻率f調(diào)節(jié)為4MHz。進(jìn)一步,根據(jù)軋輥表面微裂紋的深度分布情況,采用多道次變頻處理,即先調(diào)節(jié)所述電磁感應(yīng)裝置的較低電源輸出頻率,主要鈍化、焊合深度較深的微裂紋;后調(diào)節(jié)所述電磁感應(yīng)裝置的較高電源輸出頻率,主要鈍化、焊合深度較淺的微裂紋,使輥面不同深度的微裂紋均能得到有效感應(yīng)處理。調(diào)節(jié)所述電磁感應(yīng)裝置的電源輸出電壓,控制軋輥表面層內(nèi)的感應(yīng)電流強度,進(jìn)而控制軋輥表面溫度。進(jìn)一步,對于微裂紋均勻分布于整個軋輥表面,所述電磁感應(yīng)裝置為圓環(huán)型感應(yīng)器,所述圓環(huán)型感應(yīng)器內(nèi)徑與軋輥輥徑相匹配,將圓環(huán)型感應(yīng)器套設(shè)在軋輥外周,從輥面一端向另一端連續(xù)均勻地對輥面整體進(jìn)行處理。進(jìn)一步,對于微裂紋只分布在輥面上的局部區(qū)域,所述的電磁感應(yīng)裝置為小型的平面型感應(yīng)器,將小型平面型感應(yīng)器靠近裂紋位置對輥面進(jìn)行處理。本發(fā)明針對軋輥使用過程在輥面產(chǎn)生的大量疲勞微裂紋,利用高頻感應(yīng)電流在裂紋尖端的“繞流”效應(yīng)和“尖端放電”效應(yīng),使軋輥表面微裂紋得到鈍化和愈合,降低軋輥磨削量,防止軋輥異常失效,從而延長軋輥使用壽命。本發(fā)明的有益效果是:(1)軋輥輥面微裂紋經(jīng)過處理后得到鈍化、愈合,增加軋輥使用時間;(2)輥面微裂紋鈍化、焊合后,可減小輥面磨削量,甚至取消部分磨削工序,降低了軋輥使用成本;(3)本發(fā)明的處理方法對輥面無接觸損傷;(4)適當(dāng)?shù)母袘?yīng)熱對消除輥面軋制硬化也有一定益處,而對正常的輥面組織無不良影響。附圖說明圖1為軋輥表面微裂紋處理裝置示意圖:圖2為帶輥面裂紋的軋輥斷面內(nèi)高頻感應(yīng)電流分布示意圖;圖3為裂紋尖端“繞流”效應(yīng)原理圖;圖4為裂紋尖端“放電”效應(yīng)原理圖;圖5為圓環(huán)型感應(yīng)器結(jié)構(gòu)示意圖;圖6平面型感應(yīng)器結(jié)構(gòu)示意圖。圖中:1高頻電源,2連接電纜,3感應(yīng)器(電磁感應(yīng)裝置),4感應(yīng)器支架,5感應(yīng)器移動裝置,6軋輥轉(zhuǎn)動裝置,7紅外測溫儀,8軋輥;31圓環(huán)型感應(yīng)器(圓環(huán)型線圈),32平面型感應(yīng)器(平面型線圈)。具體實施方式下面結(jié)合附圖和具體實施例對本發(fā)明作進(jìn)一步說明。一種軋輥表面微裂紋的處理方法,在有微裂紋的軋輥表面通過電磁感應(yīng)裝置在軋輥表面產(chǎn)生感應(yīng)電流,利用感應(yīng)電流使裂紋尖端位置局部得到加熱升溫,鈍化裂紋尖端,并且在裂紋尖端能焊合微裂紋,使軋輥表面微裂紋得到愈合。參見圖1,一種軋輥表面微裂紋的處理裝置,包括高頻電源1、連接電纜2、感應(yīng)器3,感應(yīng)器支架4、感應(yīng)器移動裝置5、軋輥轉(zhuǎn)動裝置6、紅外測溫儀7;電磁感應(yīng)裝置主要由高頻電源1、感應(yīng)器3組成,高頻電源1經(jīng)連接電纜2連接感應(yīng)器3,高頻電源1可調(diào)頻,調(diào)頻范圍為0.5~10MHz;所述感應(yīng)器3包括圓環(huán)型線圈31、平面型線圈32,線圈匝數(shù)1~2匝。軋輥8被水平置于軋輥轉(zhuǎn)動裝置6上,感應(yīng)器3靠近軋輥8表面,感應(yīng)器3安裝在感應(yīng)器支架4上,感應(yīng)器支架4固定在移動裝置5上,在軋輥8上方還安裝有紅外測溫儀7,紅外測溫儀7主要目的是對軋輥輥面溫度起監(jiān)控作用。軋輥整體處理時,感應(yīng)器3為圓環(huán)型線圈31,感應(yīng)器線圈匝數(shù)1~2匝,參見圖5,感應(yīng)器3套設(shè)在軋輥8外周,感應(yīng)器3最初處于軋輥8輥面的一端位置,軋輥轉(zhuǎn)動裝置6以勻速w轉(zhuǎn)動軋輥8,啟動高頻電源1,高頻交變電流通過連接電纜2在感應(yīng)器3內(nèi)流動,并在軋輥8表面層內(nèi)感應(yīng)出渦電流,依靠渦電流對軋輥8輥面微裂紋開始處理。同時,感應(yīng)器3通過感應(yīng)器移動裝置5向軋輥另一端勻速V移動,這樣整個軋輥輥面微裂紋得到均勻地鈍化、愈合處理,改善了輥面性能。軋輥局部處理時,感應(yīng)器3為平面型線圈32,感應(yīng)器線圈匝數(shù)1~2匝,參見圖6,感應(yīng)器3靠近軋輥8表面,對裂紋位置局部進(jìn)行處理。本發(fā)明的軋輥表面微裂紋的處理方法,是在有微裂紋的軋輥表面通過電磁感應(yīng)裝置引入感應(yīng)電流,利用感應(yīng)電流在裂紋尖端存在的“繞流”效應(yīng),參見圖3,使裂紋尖端位置局部得到加熱升溫,鈍化裂紋尖端,有效降低材料裂紋進(jìn)一步擴展趨勢。而且在裂紋尖端存在“尖端放電”效應(yīng),原理如圖4所示,電荷不斷積累,以至擊穿裂紋內(nèi)氣隙而放電,可以焊合微裂紋,使軋輥表面微裂紋得到愈合。這些均有助于減小軋輥磨削量甚至取消部分中間磨削,延長軋輥使用壽命。調(diào)節(jié)所述電磁感應(yīng)裝置的電源輸出頻率,使感應(yīng)電流在軋輥表面的集膚深度δ與微裂紋的深度d基本相當(dāng),參見圖2,過大則加熱深度過大,電耗增加,且對軋輥表層微觀組織狀態(tài)有不良影響,不利于軋輥后續(xù)繼續(xù)工作;過小則適合處理的裂紋深度變小,對大而深的裂紋處理效果降低。集膚深度δ可按照δ=1/sqrt(π*μ*σ*f)來近似計算,其中μ是導(dǎo)體(軋輥)磁導(dǎo)率,σ是導(dǎo)體(軋輥)電導(dǎo)率,f是所施加的交流電頻率。取高溫下軋輥磁導(dǎo)率μ=4π×10-7Ω·m,電導(dǎo)率σ=0.75×106S/m,不同頻率f下輥面集膚層深度δ如表1所示:表1f,(MHz)0.51234510δ,(mm)0.820.580.410.340.290.260.18對于0.1~0.3mm深的軋輥表面疲勞微裂紋,所述電磁感應(yīng)裝置的電源輸出頻率f調(diào)節(jié)為f=4MHz。調(diào)節(jié)所述電磁感應(yīng)裝置的電源輸出電壓,控制感應(yīng)器線圈內(nèi)電流強度,可以控制軋輥輥面所處的電磁場強度,并控制軋輥表面層內(nèi)的感應(yīng)電流強度,確保既不過分加熱輥面層,使輥面溫度過高,這樣會改變軋輥表面的微觀組織,降低輥面硬度,甚至輥面嚴(yán)重氧化,不利于軋鋼后續(xù)繼續(xù)工作;同時,在裂紋尖端處的感應(yīng)電流聚集強度足夠大,以在裂紋尖端局部發(fā)熱,對裂紋進(jìn)行鈍化、焊合處理,而沒有裂紋的正常輥面位置則發(fā)熱并不大。如果對輥面溫度進(jìn)行紅外監(jiān)控,輥面加熱溫度絕對不能超過500℃,優(yōu)選的,軋輥輥面溫度控制在200℃左右,這樣還可以在一定程度上消除軋輥輥面在軋制過程產(chǎn)生的加工硬化問題。根據(jù)輥面的微裂紋位置分布情況,具體分兩種方式進(jìn)行處理:(1)整體處理,即微裂紋均勻分布于整個輥面,采用大型的與軋輥輥徑匹配的圓環(huán)型感應(yīng)器,套設(shè)在軋輥外周,從輥面一端向另一端連續(xù)均勻地對輥面整體進(jìn)行處理;(2)局部處理,即微裂紋只分布在輥面上的一些局部區(qū)域,例如,裂紋主要分布在與帶鋼邊部接觸的輥子兩端,或其他輥面局部位置,依靠無損探傷檢測出微裂紋存在的具體位置后,采用小型的平面型感應(yīng)器,靠近裂紋位置對輥面進(jìn)行處理。根據(jù)軋輥表面微裂紋的深度分布情況,處理時采用多道次變頻處理,即先調(diào)節(jié)所述電磁感應(yīng)裝置的較低電源輸出頻率,主要鈍化、焊合深度較深的微裂紋;后調(diào)節(jié)所述電磁感應(yīng)裝置的較高電源輸出頻率,主要鈍化、焊合深度較淺的微裂紋,這樣使輥面不同深度的微裂紋均能得到有效感應(yīng)處理。實施例1:整體處理微裂紋均勻分布于整個輥面,感應(yīng)器3采用圓環(huán)型感應(yīng)線圈31,其結(jié)構(gòu)如圖5所示,感應(yīng)線圈31套設(shè)在軋輥8外周,并與連接電纜2和高頻電源1連通,感應(yīng)線圈31內(nèi)部通水冷卻,軋輥8水平置于轉(zhuǎn)動裝置6上,感應(yīng)線圈31的匝數(shù)為1匝,并通過感應(yīng)器支架4把感應(yīng)線圈31固定在感應(yīng)器移動裝置5上。感應(yīng)線圈31最初放在軋輥8輥面一端位置。打開高頻電源1,調(diào)節(jié)高頻電源1至工作頻率2MHz,高頻交變電流通過連接電纜2在感應(yīng)線圈31內(nèi)流動,并在軋輥8表面感應(yīng)出電流,對軋輥8輥面微裂紋開始處理。同時,通過軋輥轉(zhuǎn)動裝置6帶動軋輥8轉(zhuǎn)動,w=100rpm,使輥面周向微裂紋得到均勻處理。感應(yīng)線圈31通過感應(yīng)器移動裝置5從軋輥8一端向軋輥8另一端勻速移動,V=0.2mm/s,這樣整個輥面軸向分布的微裂紋得到處理。采用三道次變頻處理,第一道次電源頻率0.5MHz,第二道次電源頻率3MHz,第三道次電源頻率10MHz,這樣使輥面不同深度的微裂紋都能得到處理。紅外測溫儀7測量軋輥輥面的溫度信號,并和高頻電源1閉環(huán)控制,防止輥面溫度過高而損傷輥面,處理輥面溫度上限設(shè)定為180~200℃。實施例2:局部處理微裂紋分布于輥面局部位置,依靠無損探傷對裂紋定位后,采用平面型感應(yīng)線圈32,其結(jié)構(gòu)如圖6所示,其余裝置與實施例1中相同,平面線圈32靠近輥面裂紋位置,調(diào)節(jié)電源1電參數(shù)使之與感應(yīng)線圈負(fù)載阻抗相匹配,保證電源系統(tǒng)處于最佳工作狀態(tài),最后升高電源1輸出電壓,對輥面的裂紋進(jìn)行局部感應(yīng)處理。以上僅為本發(fā)明的較佳實施例而已,并非用于限定本發(fā)明的保護(hù)范圍,因此,凡在本發(fā)明的精神和原則之內(nèi)所作的任何修改、等同替換、改進(jìn)等,均應(yīng)包含在本發(fā)明的保護(hù)范圍之內(nèi)。